A Blueprint for a Greener Future
5 strategies for reducing environmental impact
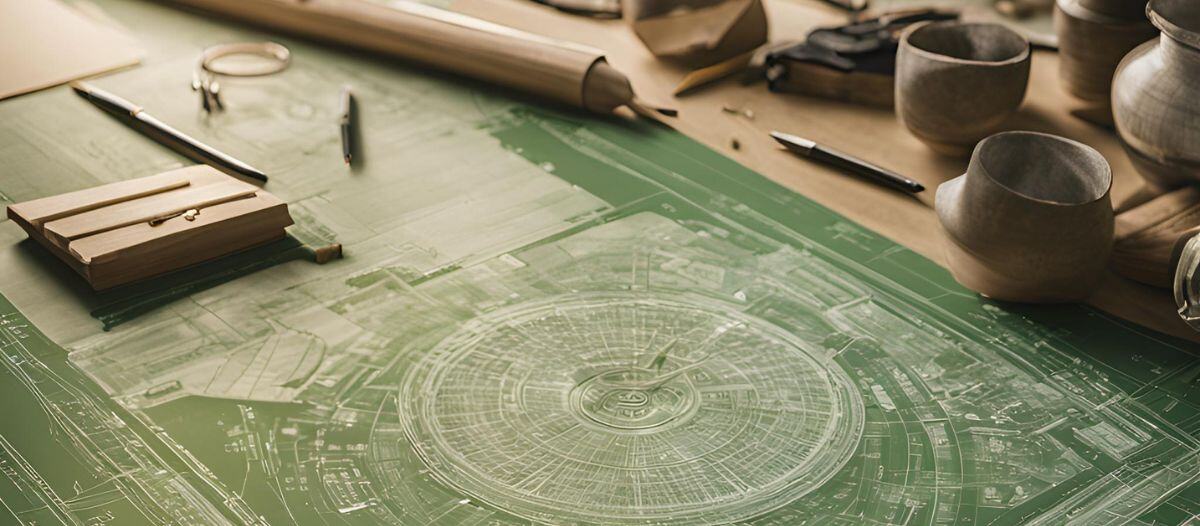
According to the U.S. Environmental Protection Agency’s (EPA) data on durable goods, furniture is one of the least recycled goods in the United States, with 17 billion tons of office furniture sent to landfills annually. As organizations grapple with the growing environmental crisis, it is clear that this massive disposal problem is a crucial issue for the commercial real estate industry and the global facilities and AEC (architecture, engineering and construction) industries.
Facility owners, project managers and designers are uniquely positioned to address this waste by implementing strategic planning in furniture, fixtures and equipment (FF&E) procurement. By adopting sustainable furniture practices, organizations can move toward a more circular economy in which waste is minimized, resources are conserved and economic and environmental benefits are maximized.
Organizations can follow five critical pillars of sustainable furniture planning to reduce environmental impact: understanding material transparency and certifications, evaluating manufacturing partners, integrating sustainability requirements into specifications, embedding sustainability criteria into requests for proposals (RFPs), and shifting mindsets and behaviors for long-term change.
1. Understanding material transparency & certifications
One of the most critical aspects of sustainable furniture planning is understanding the materials used in the products being sourced. Chemicals used in furniture manufacturing, such as flame retardants, volatile organic compounds (VOCs), and per- and polyfluoroalkyl substances (PFAS), can pose significant health and environmental risks. These chemicals can bioaccumulate in human bodies and ecosystems, leading to long-term chronic health problems and environmental damage.
To address this, facility managers and project planners should prioritize material transparency and look for products certified by credible third-party organizations. Certifications such as BIFMA Level, Cradle to Cradle Certified (C2CC), Declare and Environmental Product Declarations (EPDs) offer transparent data on a product’s environmental and health impacts, including factors like material health, product circularity, water stewardship and social fairness. By specifying furniture that meets these certification standards, organizations can ensure that their purchases align with sustainability goals and avoid greenwashing (false claims of environmental friendliness).
Just One Thing*:
-
Opt for furniture with third-party-verified certifications that promote transparency and avoid harmful chemicals.
-
Prioritize renewable, nontoxic, responsibly sourced materials like hemp-based or sugarcane-based textiles and biobased materials.
*What’s Just One Thing, or JOT for short? Which solutions suit an organization’s goals and values? Start with Just One Thing to take an important step toward a greener, cleaner world.
2. Evaluating manufacturing partners & practices
The journey toward sustainable furniture planning does not end with material transparency. Another crucial component is evaluating manufacturing partners. Manufacturing processes and logistics directly impact a product’s carbon footprint. FMs should work with manufacturers prioritizing sustainability in production methods and logistics, such as sourcing local products and materials to reduce transportation emissions. Additionally, thoughtful installation planning can minimize waste and optimize resources, further contributing to an eco-friendlier footprint.
Sustainable manufacturers invest in renewable energy sources, reduce waste and greenhouse gas emissions, and implement circular production practices, such as take-back programs that allow products to be returned and repurposed at the end of their life. Manufacturers with strong environmental, social and governance (ESG) programs often align with an organization’s sustainability goals, providing transparent, data-driven reporting on their progress. This level of clarity is essential, as transparency helps organizations distinguish genuine sustainability efforts from greenwashing: the use of vague, marketing-driven claims that lack substantiated impact. Clear reporting empowers FMs to make informed decisions based on measurable actions rather than superficial promises.
Organizations can ensure that the products they procure contribute to a greener supply chain by establishing partnerships with manufacturers committed to reducing their environmental impact.
Just One Thing:
-
Seek out manufacturers who demonstrate a commitment to sustainability through ESG reporting, third-party certifications and innovative, low-impact manufacturing processes.
-
FMs, with their influential voice, can drive meaningful progress toward sustainability by engaging directly with the industry to foster change and actively assess manufacturers' commitment to long-term environmental objectives.
3. Integrating sustainability into specifications
Product specifications are the backbone of any FF&E project. The decisions made at the specification stage dictate the sustainability of a project in terms of the materials, design and life cycle of the furniture being procured. FMs must incorporate sustainability into their specifications to ensure that their selected products meet environmental and operational requirements.
Focusing on durable, repairable and modular products is essential when specifying furniture. This approach supports a circular economy by extending the product's life and reducing waste, as repairs and upgrades can be made instead of total replacements, keeping materials in use for longer and minimizing environmental impact. To significantly lower a project's carbon footprint, choose furniture made from recycled or recyclable materials and incorporate second-life or refurbished products.
Consideration should also be given to the logistics of furniture delivery and installation. Opting for flat-packed furniture shipped in minimal packaging reduces waste and transportation emissions. Additionally, look for suppliers who use biodegradable or reusable packaging materials and offer recycling programs for furniture at the end of its life cycle.
Just One Thing:
-
Specify durable, modular furniture that can be multipurpose, flexible, and can be repaired and reused, reducing the need for replacements.
-
Prioritize products made from recycled or recyclable materials and consider second-life or refurbished furniture for lower-impact solutions.
4. Embedding sustainable criteria in RFPs
Sustainability in FF&E procurement is not just about the products themselves but also about the processes used to acquire them. Embedding sustainable criteria into RFPs is a powerful way to signal the organization’s commitment to sustainability and drive meaningful change across the supply chain.
When drafting an RFP, FMs should include specific requirements for sustainability. This might involve asking vendors to provide detailed information on the environmental impact of their products, including certifications, material sourcing and manufacturing practices. They can also request information on the vendor’s ability to support circular economy initiatives, such as take-back programs and product recycling.
A well-structured RFP should also evaluate vendors based on their sustainability credentials, using a weighted scoring system to ensure that environmental considerations are given due importance alongside cost, quality and performance history. Organizations can select vendors that align with their environmental and social objectives by setting clear expectations for sustainability in the RFP process.
Just One Thing:
-
Include sustainability requirements in RFPs, asking vendors to provide certifications, material transparency and details on their environmental practices.
-
Use a weighted evaluation process that prioritizes sustainability alongside cost and functionality.
5. Shifting mindsets and behaviors for lasting change
Sustainability is more than short-term, eco-friendly choices; it fosters a lasting cultural shift toward responsible consumption and procurement practices. This requires changes in processes, policies and, most importantly, a shift in organizational mindset.
Indeed.com, an online job search engine and employment website that connects job seekers with employers, prioritized environmental responsibility while constructing a 36-story tower in downtown Austin, Texas, USA. They partnered with local vendors to develop creative, sustainable solutions in response to pandemic-induced budget constraints. Indeed.com repurposed 70 percent of its furniture through strategic planning by decommissioning and reconfiguring workstations from another local facility. They also eliminated nonessential design elements, reused gym equipment and greenery, and used new accessories to seamlessly blend old and new elements. This approach aligned with their sustainability goals and saved seven figures through reusing assets.
Indeed.com further developed a program to evaluate manufacturers based on sustainability criteria, categorizing them into good, better, best and fail. This transparency drives procurement decisions and pushes suppliers toward higher standards. By sharing their criteria with manufacturers, Indeed.com ensures they know exactly what is required to earn business. As a result, they are on track to source 95 percent of new furniture from their “best” category by 2025.
Creating a culture of sustainability involves engaging leadership and employees alike. According to the 2023 World Economic Forum’s Future of Jobs Report, leadership buy-in is critical for driving sustainable change; but engaging employees at all levels is equally important, especially as the next generation of decision makers increasingly seeks organizations that prioritize ESG goals. Studies show that younger leaders value sustainability and social responsibility, making it essential to embed these practices across the organization. Establishing green teams or sustainability committees can help champion these values, ensuring they are embedded into daily operations. Ongoing education and training are also essential for building awareness and equipping employees with knowledge of sustainable practices, from material selection to waste reduction.
Measurable goals and celebrating successes further strengthen a sustainable culture. Tracking progress and highlighting the environmental, financial and social benefits of sustainable choices reinforce their importance and inspire continued commitment.
Just One Thing:
-
Engage leadership and employees in sustainability initiatives through committees, education and a culture of continuous improvement.
-
Set measurable sustainability goals, track progress and celebrate achievements to drive long-term change.
By focusing on these five pillars — material transparency, manufacturing practices, specifications, RFP criteria and behavioral shifts — organizations can transform their FF&E procurement processes into a blueprint for a greener future. Sustainable furniture planning and programs reduce environmental impact and align with broader organizational goals around corporate responsibility, social equity and financial efficiency. The journey toward sustainability is ongoing, but with planning and a commitment to circular principles, FMs can create a future where furniture is part of the solution, not the problem.
As facility owners and project managers continue exploring innovative ways to reduce waste and minimize environmental impact, these strategies provide a practical roadmap for achieving environmental and business objectives. One chair at a time, FMs can make a difference.
According to the EPA’s data on durable goods, furniture is one of the least recycled goods in the U.S., with 17 billion tons of office furniture sent to landfills annually. It is up to facility owners and project managers to lead eco-nomic and eco-friendly strategies to reduce waste and drive toward a more circular economy.
There are five pillars of sustainable furniture planning including:
-
understanding material transparency and certifications,
-
evaluating manufacturing partners and their practices,
-
integrating sustainability requirements into specifications,
-
integrating sustainable product requirements into Requests for Pricing (RFPs) and
-
shifting mindset and behaviors for lasting change.
By adopting these approaches, organizations can lower their carbon footprint, support a circular economy and meet both environmental and business objectives.
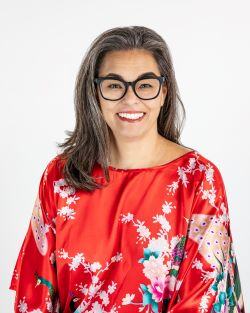
Dianne Murata is the founding principal and accidental environmentalist at kimiko designs, an interior design firm specializing in all things furniture (except selling it). kimiko designs leads kimiko green, a community of industry experts, including Toyota North America, Sony Pictures Entertainment, Zions Bancorporation, Los Alamos, and Indeed, partnering to envision a better way to manage the furniture waste created by the built environment.
Read more on Sustainability , Leadership & Strategy and Real Estate
Explore All FMJ Topics