Case Study: Unearthing Savings
The hidden value of a warranty program
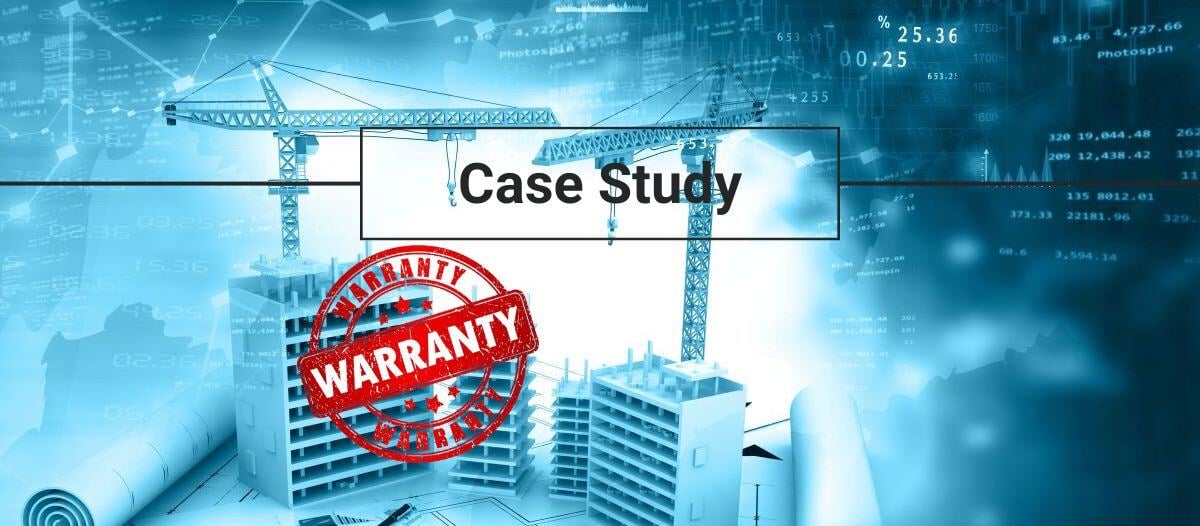
A modest resource investment to create a warranty program can pay for itself many times over in cost avoidance while improving asset management.
Almost everyone has experienced the situation where a recently purchased, high-priced item fails or becomes defective, which is followed by a substantial repair bill or the need to replace equipment. Before taking out a credit card or a loan, most consumers first determine whether the item is under warranty. The same holds true in an organizational environment. Investing in a warranty program brings many benefits to an organization. Having an intentional approach to tracking warranties can lead to cost avoidance by leveraging contractor or manufacturer warranties. Additionally, a warranty program with centralized support can enhance contractor relations and improve overall quality performance and accountability.
Background
Prior to the implementation of Sandia National Laboratories’ warranty program, pursuing warranties was an ad hoc process, at best. There was no established system or process in place to effectively manage and track warranty obligations. Attempting to pursue warranties without the necessary tools, measures, or resources hindered staff’s ability to accomplish this effectively. This led to organizational inefficiencies, as well as wasted time and resources as new equipment had to be replaced or repairs had to be paid for a second time. It was often difficult to determine who was responsible for the rework, causing missed potential benefits from contractor or manufacturer warranties.
The idea for a warranty program was pitched to leadership with a proposal to add an additional team member who would focus solely on managing and pursing warranties. This individual would be responsible for managing the entire warranty process, including tracking and validating warranties, coordinating with stakeholders, and documenting and reporting on warranty pursuits. The goal was that this position would pay for itself, many times over, by cost avoidance from pursuing warranties. This centralized support position would provide warranty expertise to correct facility issues that are under contractor or manufacturer warranties across the infrastructure and building envelopes. Management approved the creation of a warranty coordinator position, and the new program implementation was initiated from scratch.
Roll-out of warranty program
Implementation of the new program involved developing a vision of the future program, conducting stakeholder interviews, and identifying the deliverables required to successfully implement the program. Key areas included establishing a knowledge base, defining the program scope, developing effective communication strategies, outlining the processes for warranty pursuits and gathering the warranty information. These steps formed the foundation for the program's implementation and ensured a comprehensive approach to managing the warranties.
Key core elements
The warranty program consists of four key core elements: governance, process, tools and training.
Governance: Governance for the warranty program is a contractual requirement, encompassing the formal written contract, including the statement of work and terms and conditions. Various types of warranties exist, such as general contractor warranties (typically one year), installer warranties (two to five years years), manufacturer warranties with varying durations (e.g., motor warranties for one to two years, heat exchanger warranties for 10 years, thermoplastic polyolefin (TPO) roof warranties for up to 30 years), and extended warranties (e.g., chiller warranties for five years covering labor, parts and refrigerant). Verbal or handshake contracts are not acceptable for warranties. Accountability and the need for an effective partnership was emphasized, which would spell out obligations between two sides.
Owner obligations: The owner’s obligations include confirming that every item is covered under the contract and within the warranty period. Pursuing items out of warranty is not appropriate. Validating the warranty letter’s coverage of time is crucial, as some warranty letters may expire sooner rather than later. The owner is responsible for validating the failed or defective item, ensuring it falls within the scope of work and the warranty period.
Warrantor obligations: When the owner sends a warranty notification, the warrantor must confirm receipt of the notification and promptly repair any failure, defect or damage. The warrantor provides updates on the warranty status of repairs until completion. The warrantor is obligated to inform the owner if the failed or defective item is not considered to be warranty-related or if they are unable to replace or perform the repairs.
Process: The workflow process is essential for the success of the warranty program. This 7-step process includes identifying warranty issues, initiating pursuits, and managing them through resolution.
- Notification of a failed or defective item: The organization uses a computerized management maintenance system (CMMS) tool to flag the item with a bold red-letter notification indicating the existence of a warranty.
- Verify warranty exists: Confirm that the failed or defective item is covered under warranty by checking the project documents, including the statement of work and designs. Ensure that the warranty terms and conditions align with the specific item in question.
- Reasonably validate: Engage the validation team, including craft personnel, engineers, inspectors, facility/building managers and subject matter experts (SME), to reasonably validate the warranty claim.
- Notify warrantor: Send a notification to the warrantor with all the necessary details, including the location, project information, timeliness, and contacts. Note that the notification is not contract direction; it is for informational purposes only.
- Track/document response activities: Document the response activities in the CMMS tool, specifically in the work logs, to track the progress and status updates.
- Warrantor completes work: The warrantor carries out the necessary work to address the warranty claim and provides confirmation that the work is completed.
- Validate to completion: Validate with the original validation team member that the work has been satisfactorily completed and meets the required standards.
This process ensures that warranty claims are effectively managed and tracked, providing a consistent and reliable approach to warranty management.
Upon completion of all seven steps, the warranty coordinator sends the completed scope of work to the professional estimator for cost avoidance calculations. Additional elements to the warranty program include procedures, work instructions, job aids and adherence for consistency and sustainability.
Tools: The warranty coordinator position uses the CMMS tool for tracking and maintaining warranties. CMMS provides the essential capabilities of digitally tracking warranties, capturing cost avoidance by using key performance indicators, initiating communication with contractors and manufacturers, and monitoring overall warranty program performance. The CMMS platform contains a warranty application that proved to be necessary to incorporate into the warranty program. This application provides several options to enter detailed warranty information. One part of the terms and conditions of a warranty letter states the timelines involved. Manufacturer letters specify a required notification period. For example, a TPO warranty may require the reporting of any leaks within 10 or 30 days. These timelines are entered into the CMMS tool and are used to report on a timely basis for warranty pursuits.
Training: The final element of the program is training. Training is crucial for the success of the warranty program. It plays a vital role in ensuring that all stakeholders are knowledgeable about the process and their responsibilities. Training sessions are conducted with various departments, including the facility area, warehouse, maintenance teams, planners, project managers, construction managers, SMEs, craft, and inspectors. These sessions have provided a comprehensive understanding of how the system works (e.g., warranty policies, procedures, use of CMMS tools), and the importance of the stakeholder’s role in identifying and reporting warranty items.
An example of how the core elements work
An actual warranty example that recently occurred during a preventive maintenance walk-through identified an issue with a chiller. A craft member knew this item was a newly installed chiller and contacted the warranty coordinator. The asset number was provided and checked in the CMMS tool, which flagged it for being under warranty. The craft provided validation, and a warranty notification sent to the contractor to correct the issue. The contractor conducted troubleshooting and found a leak at the relief valve on the chiller. The refrigerant was drained, the relief valve replaced, and the refrigerant was replenished. The contractor confirmed the completion of the work, and the craft validated it was complete and acceptable. Notably, this warranty was expiring the following week. As demonstrated in this example, the warranty program follows a well-defined, sustainable, consistent, and robust process.
These core elements are important as they are all interconnected and form an integrated system for executing warranty activities throughout the entire warranty life cycle.
Program Benefits
The organizational warranty program has delivered tangible benefits, including improved quality awareness, enhanced specifications, streamlined closeout processes and substantial cost avoidance.
- Significant cost avoidance: Cost avoidance, in its simplest term, is money that did not have to be spent on repairs or replacements due to pursuing an already existing warranty. All estimated warranty labor and material is calculated by a professional estimator and is recorded in the CMMS tool, allowing for easy calculation of reportable costs. In five years, a remarkable cost avoidance of US$2.6 million has been achieved through the warranty program. This accomplishment is a testament to the program's effectiveness.
- Over the course of five years since the deployment of the warranty program, the organization has collected helpful data. For example, the data has revealed which functional areas have the most warranty pursuits.
- Mechanical, Electrical, and Plumbing: 35 percent
- Roofing: 32 percent
- Structural:17 percent
- Other: 16 percent
- Stakeholders are made aware of the program and actively engage in pursuing warranties. Craft are more comfortable in inquiring about and reporting warranty-related issues now that there is a centralized support person in place.
- Effective communication has been established across the organization, including with contractor partners, to ensure that everyone is aware of the warranty program and its expectations. This helps improve stakeholder awareness and ensures aligned expectations throughout the process.
- With the data collected since the program went live, the organization has made several improvements to its contractor construction specifications. In many cases, the warranty periods have been extended. Previously, the TPO warranty offered a 20-year material-only pro-rated coverage. A transition to a 20-year, no dollar limit warranty has proven to be highly effective and beneficial.
- Process improvements have been incorporated into the program. For example, the closeout process now ensures alignment with the requirements of the warranties provided. A comprehensive sample warranty letter has served as a valuable template for effective communication and documentation. This standardized letter facilitates concise communication with contractors, suppliers, and other stakeholders involved in the warranty letter submittal.
This program serves as a valuable addition to the organization, not only in terms of cost savings but also in fulfilling the organization’s mission.
Lessons learned
Five years after implementing the warranty program, valuable lessons contributing to the program’s success have become apparent.
- Ensuring stakeholder alignment and support from stakeholders across the organization was crucial in enabling it to effectively pursue warranties. This involved engaging and communicating with various departments and individuals throughout the organization.
- Loading contracts into the CMMS tool and flagging them for warranty allowed the organization to easily identify items that may be under warranty, with the system highlighting them in red for quick recognition.
- Thoroughly understanding contracts and statements of work ensured compliance to effectively use warranties. This involved studying relevant regulations and seeking clarity on warranty-related information.
- Building trust and establishing a central point of contact for warranty pursuits helped create transparency and fostered collaboration among craft, construction managers, and the warranty coordinator. This cultural shift facilitated smoother warranty processes and improved program effectiveness.
- Involving inspectors in the warranty program and requiring them to review completed work ensures that warranty-related work is validated to the standards necessary for completion.
- Increasing awareness of the warranty program among project teams ensures they proactively reach out to the warranty coordinator to avoid cancelling active warranties. This ensures proper execution of the warranty program and avoids potential warranty issues during project execution.
Using in-house estimators for warranty pursuits ensured accurate and detailed estimates of warranty-related work.
These lessons highlight the importance of stakeholder alignment, process refinement, understanding contracts, and use of internal expertise. Having a warranty program within the organization’s facilities operations saves the organization time and money.
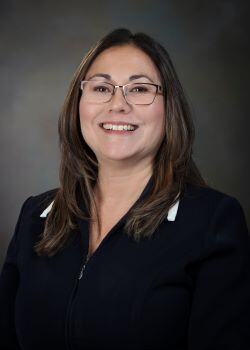
Gloria Hill is the Program Lead for the Facilities Warranty Management Program at Sandia National Laboratories. With more than 20 years of experience at Sandia, she has gained expertise in a wide range of areas including property management, training, human resources, finance, contracting and international programs. In her role, she has demonstrated her capabilities by successfully developing and implementing a warranty program. Her diverse background and extensive experience have equipped her with the skills and knowledge necessary to drive the success of the program.
Read more on Finance & Business , Operations & Maintenance and Project Management
Explore All FMJ Topics