Institutional Knowledge
5 steps to preserve & maximize veteran know-how
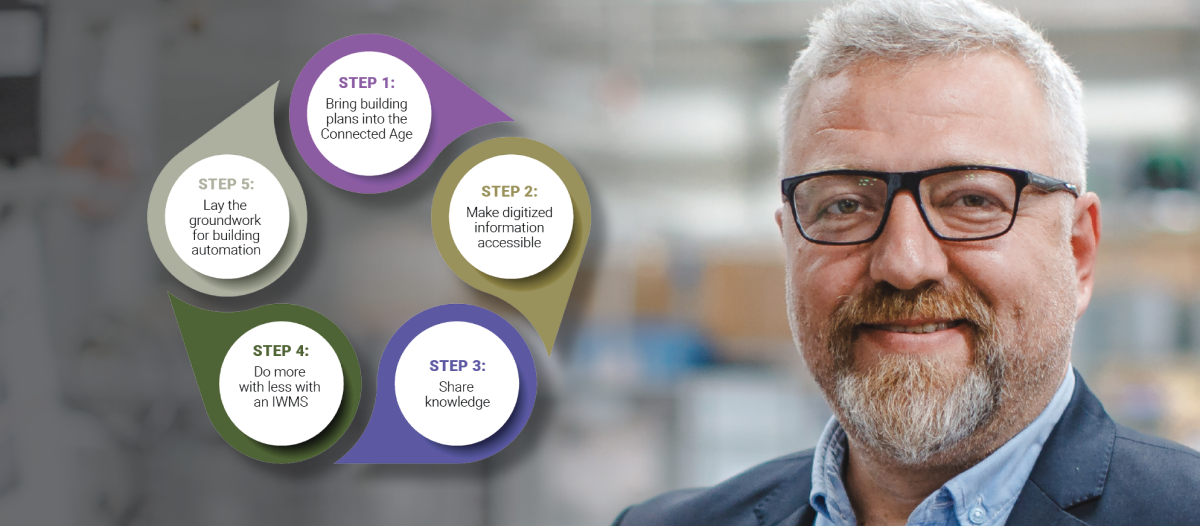
That is the reality many organizations are facing as FMs age out of the profession. The average age of facility managers is 50, according to analysis by Zippia, and enticing younger workers into the profession has been a challenge in the industry for years. Even if FM suddenly became the hot new profession, it is unlikely new candidates would be prepared to fill the shoes of the FMs lost to retirement. A recent survey found that 86 percent of FM managers recognized a knowledge gap between their teams’ current skills and what is needed to excel. That discrepancy stems primarily from a mismatch between the skills future FMs are taught in college and the skills they will actually use on the job.
Fortunately, FM’s Great Retirement is coinciding with great advancements in FM technology. Here are five steps FMs can follow, and technology they can adopt to ensure that the coming wave of retirements and ongoing skilled labor shortage do not degrade their ability to operate and maintain the buildings in their care.
Step 1: Bring building plans into the Connected Age
After decades on the job, FMs nearing retirement are treasure troves of skill and know-how. That knowledge has been accrued over the years in a variety of ways, including classroom learning and mentoring from colleagues and predecessors. But when it comes to attaining a deep understanding of the ins and outs of a specific building or portfolio, much of that information will have come from rifling through reams of paper plans, reports, logs and permits.
Each building is a unique and complex combination of materials, components, and equipment. Over the years, an FM may commit to memory the location of every duct, valve and pipe. That depth of knowledge and familiarity is irreplaceable, which is both laudable and alarming. When the intricacies of a building are only accessible from two places – one that may walk out the door at any time and one that can easily be lost, damaged or destroyed – that sets the stage for the type of snowballing calamity described above.
Despite a longstanding push across many industries to go paperless, many FMs still rely on paper documentation as a backup knowledgebase for industry veterans. As such, one of the first and most important steps organizations can take is to digitize essential documents like floor plans, permits, maintenance logs and inspection schedules and reports. Veteran FMs should also be asked about the knowledge they have accumulated that is not recorded in that documentation to make sure it is preserved digitally. Questions to consider might include:
- Are there any substantial differences between how the electrical, HVAC or plumbing systems are recorded on paper and how they are actually laid out in the building?
- What piece of building equipment is most in need of replacement? Why?
Step 2: Make digitized information accessible securely anytime, from anywhere
Where digitization has been attempted, it has often taken the form of only the most important documents being scanned and saved on a laptop or thumb drive. This method restricts access to one person at a time and increases the risk of losing or erasing the data. Organizations that are serious about planning for the coming wave of FM retirements and the ongoing skilled labor shortage need to create a priority list for digitization that, in the end, results in almost all paper documentation being preserved electronically.
As paper records are converted into digital formats, that information should be uploaded into an integrated workplace management system (IWMS) where it can be centrally managed and secured. FM software, like IWMS, also can provide quick access to key equipment data for building assets that need to be maintained. This allows organizations to improve equipment performance and longevity, reduce downtime, and decrease costs by efficiently managing technicians, measuring performance against service level agreements, and identifying under-performing areas.
Consolidating digitized and digital information in a facility management solution enables stakeholders to access it from anywhere, at any time, while protecting it from accidental erasure or tampering. Making crucial details easy to find can not only help keep small issues from becoming big problems, but also allow FMs and technicians to work more efficiently, empower first responders to deal with emergencies more effectively, and streamline tasks related to permitting, inspections and compliance reporting.
Finally, keeping all essential information in a single software repository enables FMs to leverage that data for a wide variety of other uses and initiatives.
Step 3: Sharing knowledge empowers
Once paper documentation is digitized and combined with other data in the IWMS, that knowledge can be disseminated and transferred in structured and strategic ways. For example, succession plans for retiring staff should include a review of the information in the repository and how to access it.
The consolidated data can also be organized and curated to help with upskilling new workers and closing the knowledge gap between what new entrants into the FM field learn in college and the skills they will need to do their job. Digitized information accessible through FM software can supplement mentor-apprentice initiatives and form the basis for training and development, helping to ensure that crucial building- and portfolio-specific details get passed down from retiring FMs to their replacements.
Step 4: Do more with less with an IWMS
FM systems are excellent at preserving FM know-how and making important information easily accessible for training and development, but that’s not all they are good for. An IWMS can serve as the collection point for terabytes of real-time data streaming in from disparate sources, like Internet of Things (IoT) devices, smart meters, digital twins, and access control systems.
IoT devices, like environmental and occupancy sensors, can be used to optimize utilization of office space and monitor indoor air quality, which is an important factor in employee wellness, productivity and morale. Smart meters can detect water leaks, energy waste and unusual noise and vibration in equipment, negating the need to wait for something to break or cause damage before addressing it. Digital twin technology involves the creation of a virtual facsimile of essential building equipment and components that enables FMs to better plan and schedule preventive maintenance and even predict outages. Finally, access control and visitor management systems can enhance building safety and security.
This improved data collection provides the foundation for advanced reporting and analytics to help optimize building performance at the individual and portfolio level, improve space and equipment performance, and lengthen the life of facility assets to better future-proof buildings.
Step 5: Laying the groundwork for building automation
Having an FM system in place opens up a whole new world of options for addressing the dual challenges of retiring FM veterans and a dearth of young people clamoring to fill their shoes. An IWMS can serve as a resource and tool in training and developing new hires while enabling advanced reporting and insights without straining limited resources. The final piece of this puzzle is using these systems to automate key tasks that FMs previously had to handle manually, like work order ticketing and preventative maintenance scheduling and assignments.
With these smart and autonomous building solutions, FMs can deliver improved performance, increased operational efficiency and higher service levels without needing to increase headcount. As FMs embrace these innovations, the role of facility managers and the skills required to succeed in that field will evolve. While there will always be a need for FMs who are adept at hands-on tasks, the FMs of the future will also need a strong grasp of technological and analytical skills. This may finally make FMs more attractive to the younger digital natives.
At first glance, the Silver Tsunami sweeping FMs into retirement is a concerning proposition for real estate stakeholders; however, it presents an opportunity for organizations and their FM teams to significantly improve operations. In addition to addressing doomsday scenarios of flooded floors and missing code compliance documents, this transition offers a chance to enhance efficiencies and lower costs. And by embracing FM technology, organizations may even usher in a period where young professionals are clamoring for an opportunity to work in the exciting, high-tech world of FM.
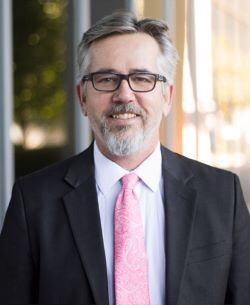
Read more on Leadership & Strategy , Project Management and Training
Explore All FMJ Topics