Objective-based Maintenance
Bridging technology & organizational goals
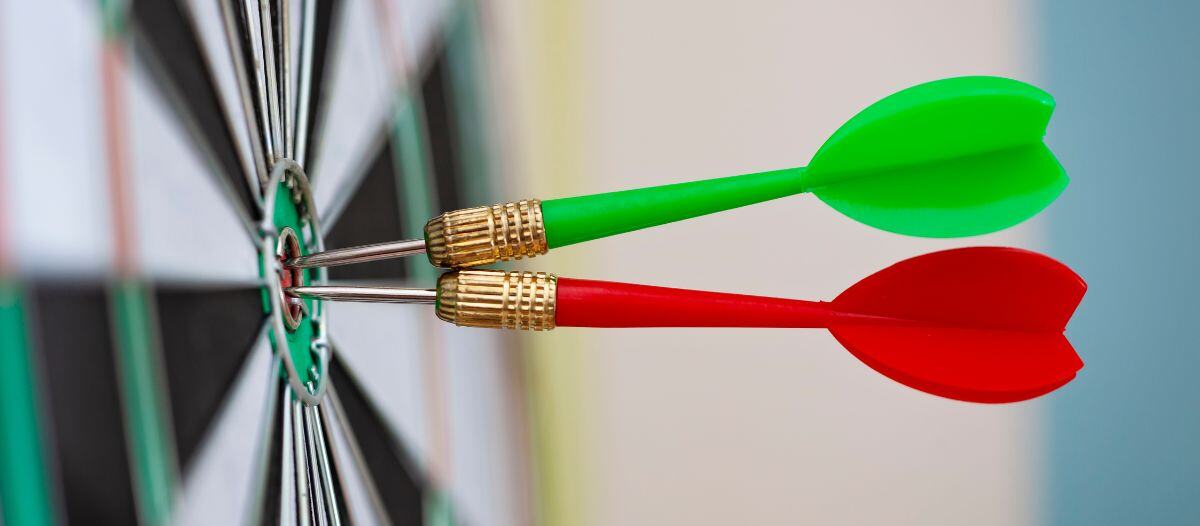
Effective asset and maintenance management, or the ability to fix the root cause of problems the first time, is crucial for the performance of a wide range of facilities, including offices, university campuses, government buildings, data centers and hospitals. Naturalist and forest conservation advocate John Muir aptly stated that when one tries to pick out anything by itself, they find it hitched to everything else in the universe. This interconnectedness is evident in the complex systems that underpin modern facilities, where one faulty component can disrupt the entire operation.
Technology plays a transformative role in enhancing the performance of complex systems. Harvard Business Review notes that smart machines help humans by amplifying cognitive strengths, interacting with customers and employees to free time for higher-level tasks and extend physical capabilities. The intersection of clear asset and maintenance objectives with technological innovation can transform maintenance processes and contribute toward growth in real estate valuations. This is the essence of objective-based asset and maintenance management.
A study from NYU Stern and Columbia University forecasts remote work and older buildings could cause U.S. office buildings to lose US$500 billion in value by 2029. While in 2023, Savills reported European office investments fell 60 percent year-over-year. According to JLL, older office towers are struggling to compete with newer buildings, which have up to 43 percent higher rents and fewer vacancies. This makes it urgent for property owners to invest in strategic initiatives such as objective-based maintenance to improve, secure and protect the value of existing building stock.
By setting clear, measurable objectives, in line with organizational goals such as achieving net zero or providing frictionless experiences, organizations can plan specific maintenance activities, track progress and prove successes. Implementing objective-based asset and maintenance management follows five stages:
-
Setting objectives
-
Aligning desired outcomes
-
Defining activities
-
Automating processes
-
Proving successes
Setting objectives
Facility and maintenance teams can often feel as if they are jumping from one maintenance emergency to another, unsure of their contribution to the organization’s overall success. Setting clear, measurable objectives is the foundational step toward resolving this uncertainty. These objectives act as a roadmap, guiding teams toward specific, actionable goals that can be tracked and measured over time. By establishing well-defined targets, organizations can identify specific actions and priorities, ensuring their maintenance strategy yields tangible benefits and drives continuous improvement.
Clear objectives provide direction and purpose, enabling facility and maintenance teams to focus on achieving specific outcomes. For instance, the U.S.-based real estate investment trust (REIT) Ventas set an ambitious goal to achieve net zero operational carbon emissions for its portfolio of 800 buildings by 2040. This objective led to the creation of 800 individual building plans, detailing specific steps, estimated costs and operational savings while keeping the established level of quality up.
Aligning desired outcomes
Facility managers might wonder how strategic organizational objectives impact maintenance teams. Isn’t it enough to keep things running and fix them when they break? By aligning objectives, organizations can translate strategic goals into actionable targets. For example, if an organization has set a net zero target, aiming to reduce facility energy consumption by 15 percent each year for the next decade, what does this mean for maintenance teams? They must ensure equipment is maintained in optimal condition, as poorly maintained equipment consumes more energy, hindering the net zero goal. Effective maintenance management is crucial for any successful energy strategy. Research conducted by the University of Reading explains: “although often viewed as independent challenges, an important interdependency exists between energy performance and the maintenance of building systems.”
Consider another scenario: an organization aims for a building occupant satisfaction score of 9 out of 10. Faulty systems, like broken heating or cooling, can lower satisfaction levels. Maintenance teams must provide timely maintenance to prevent disruptions. Setting a target to achieve a 90 percent satisfaction score after each resolved issue is a clear, measurable objective.
A final example is if an organization wants to improve critical equipment CAPEX performance. This target includes the objective to increase the average lifespan of critical equipment by 20 percent over the next five years. Maintenance technologies and processes aimed at predicting and preventing equipment failures are key to enhancing the performance and longevity of critical equipment.
It will not be possible to align every organizational objective. The aim is to achieve a balanced outcome for the building operator, user and owner. For example, reducing energy consumption while increasing building user comfort and productivity will challenge pure play energy management goals. Achieving these types of objectives requires a deeper level of collaboration to uncover the root cause of challenges and identify the best route forward.
Defining activities
After setting objectives and aligning desired outcomes, the next challenge is to get operational and define and prioritize the activities that will result in those outcomes. These activities should be captured in a digital solution that will enable maintenance teams to capture and manage data from installation to decommissioning for assets, spaces and buildings.
At this stage, it is crucial to remember that a single activity can contribute toward multiple objectives. For example, complying with the 15 percent year-over-year energy consumption reduction target mentioned above might result in maintenance activities that contribute to the organizational net zero target, the building occupant satisfaction target and the equipment CAPEX target.
Maintenance activities to achieve these objectives can be split into two categories. The first are activities aimed at prioritizing follow-up actions. The second are the follow-up actions. Prioritization activities are things such as recording observations on filters and coils to periodic system checks and adjustments. Prioritization enables automatic generation of follow-up actions. This includes activities such as filter changes or coolant leak repairs. Automating these based on prioritization will help teams avoid alarm paralysis – being overwhelmed by numerous alarms and unsure which to address first.
Automating processes
While manual maintenance activities will always be necessary, a range of automation solutions now exists to augment the capabilities of both experienced and inexperienced maintenance workforces. This is becoming increasingly important as more technicians struggle to find the information they need, with 25 percent of technicians reporting decreased operational efficiency and, on average, 21 percent higher costs to deliver services. Three key automation technologies are connected platforms, generative AI and system response automation.
-
Connected platforms. IoT-based connected platforms play a pivotal role in providing real-time data and enabling more informed decision-making processes. Building managers and service providers can use IoT devices to collect data on energy consumption, equipment performance, temperature and vibrations to quickly identify areas where issues are arising without having to walk the site to take note of performance observations.
Easier access to operational data enables organizations to optimize maintenance schedules and allocate resources more effectively by automating fault detection and diagnostics (FDD). For instance, analyzing energy consumption patterns can reveal opportunities to perform equipment corrective actions before they escalate. Peer-reviewed research finds that predictive maintenance can reduce maintenance costs by 25-30 percent and asset downtime by 35-45 percent. Having accurate, real-time data is a prerequisite for predictive maintenance that leads to more efficient operations and less time spent on reactive emergency repairs.
-
Generative AI. A subset of artificial intelligence, generative AI analyzes vast amounts of data from sources, such as IoT sensors, connected worker platforms and digital twins, to identify patterns and trends that might not be immediately apparent to human analysts. Generative AI is a powerful tool for generating actionable insights, optimizing processes and predicting future maintenance needs.
For example, generative AI can lead to broader adoption of prescriptive maintenance practices. In this use case, AI tooling will analyze real-time data, historical equipment performance data, maintenance issues and associated corrective actions, and user manuals to identify possible fault causes and suggest corrective activities. This ensures that maintenance teams are deployed efficiently, reducing the time required to identify and correct the root cause of problems.
Energy teams will benefit from the ability of generative AI to analyze energy consumption patterns and suggest activities to optimize or reduce energy usage. An energy manager can prompt an AI solution to identify which HVAC equipment is consuming more energy during off-peak hours and recommend adjustments to HVAC operating schedules. This can lead to significant cost savings and help achieve energy reduction targets. Additionally, these advancements do not require the energy manager to also be a data analyst or scientist.
The ability to generate actionable insights and predict future needs allows for a more proactive and strategic approach to maintenance, ultimately leading to better-managed facilities, longer asset life cycles, reduced CAPEX and higher satisfaction among building occupants.
-
System response automation. At the core of proactive digital maintenance strategies is the concept of system response automation. This is enabled through command center-based data analytics, which weaves together connected platforms and generative AI solutions to provide remote services for smart buildings and frontline maintenance employees. How does this work?
For certain types of maintenance issues, corrective actions can be executed immediately by automated systems. For example, if a sensor detects a significant drop in pressure within a pipeline, the system can automatically shut down the affected section to prevent damage. The system then initiates a work order with suggestions for the root cause of the problem. This shortens the time from identification of a problem to initiating corrective actions.
Additionally, in the field, technicians can use their mobile devices to query a list of activities required to pinpoint the root cause, based on prior suggestions, and fix the problem correctly the first time. By automating specific maintenance tasks and responses, organizations can optimize the use of their resources. Maintenance teams can focus on more complex tasks that require human expertise, while automated systems handle routine inspections and adjustments. This leads to more efficient use of personnel and budget toward achieving asset and maintenance management goals.
Prove success
The approach of objective-based asset and maintenance management tackles common challenges like organizational alignment and communication gaps, data collection and reporting, and personnel resourcing constraints. But what about achieving recognition for the successes of maintenance teams?
Gaining recognition begins with acknowledging the importance of setting and aligning objectives and activities. This should be done in a connected platform that integrates facilities data across maintenance, space management, sustainability and real estate. These solutions enable teams to break down operational silos to easily access and share data for reporting, business intelligence analysis and efficient alignment across departments.
With all data in one place, facilities teams are able to create compelling reports that demonstrate the value of maintenance teams to an organization. These reports will show how maintenance activities helped to extend asset lifespans by up to 50 percent, improve equipment fault detection by 20 percent, and meet rising customer experience expectations.
The reports will ensure that organizations stay aligned on overall objectives with no misunderstandings about the importance of maintenance activities. This will enable maintenance teams and their activities to gain the visibility and recognition they deserve.
Conclusion
The importance of digital asset and maintenance management solutions that can integrate advanced technologies such as IoT-based connected platforms, generative AI and system automation to achieve challenging facility goals is becoming increasingly clearer. These technologies enable organizations to translate objectives into actions, driving significant improvements in operational efficiency, cost savings and building performance. Legacy systems unable to achieve this integration will increasingly be a hindrance.
Ultimately, the integration of these technologies and strategies creates a more cohesive and efficient approach to asset and maintenance management. The ripple effects are many: maintenance teams responding faster, reduced downtime, a significant boost in stakeholder satisfaction, increased valuations. How might this change the way organizations approach not just maintenance, but the entire life cycle of building and asset management? Reflecting on these questions can reveal the profound potential of integrating siloed information sources to drive truly objective-based operational processes.
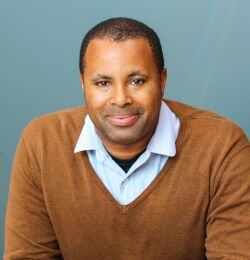
Derrek Clarke, a Registered Architect in the U.S., has worked for a range of architectural firms including global architecture, engineering and planning firm HOK. His time at HOK included the coordination of technical design and construction management for a diverse range of health care facilities. Recently, he was a senior building technology analyst with smart building research and advisory firm Verdantix in London. He is now a senior product (solution) marketer with Planon, a leading supplier of facility and field services management software, as well as IWMS and CAFM solutions. Clarke is responsible for the positioning of Planon solutions for the facility service provider market.
References
Zinier, State of Field Service Management report, What do field service technicians need to keep current?, 2020
Aquant Service Intelligence Benchmark Report, 2023
Read more on Leadership & Strategy , Technology and Real Estate
Explore All FMJ Topics