Productive Cleaning
Ensuring satisfaction while maintaining efficiency
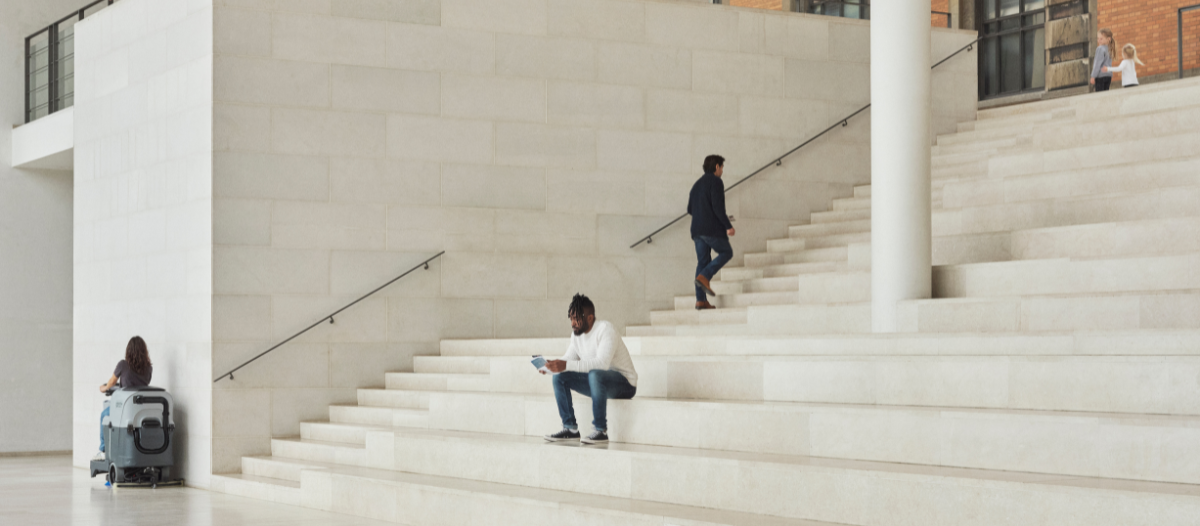
Facility managers, charged with overseeing effective cleaning operations, continue to face productivity challenges, rising employee and material costs, and increased sustainability pressures.
Cleaning operates in a higher profile in a post-pandemic world. There are expectations that public areas in a variety of settings are subject to regular and in-depth cleaning attention. This means facility operations must continue to work hard to enhance productivity, deliver quality cleaning and run a cost-effective cleaning operation.
Facility cleaning operations rely on two key assets to deliver essential cleaning services. The combination of a skilled cleaning operator and a high-performing cleaning machine solution is key to ensuring effective cleaning, which protects businesses and the public.
Traditionally, cleaning machine design has not primarily focused on operator individuality. Instead, it has typically prioritized technological advances to boost cleaning performance; but this can lead to generic solutions that undermine the operator experience and impact job satisfaction.
For example, if the machine design does not consider the operator before, during and after cleaning, essential machine maintenance becomes more difficult or potentially ignored completely. This can have a knock-on effect, resulting in unwanted and unnecessary machine downtime and productivity issues as teams struggle to complete cleaning tasks on time.
Machine design to support the workforce
Cleaning operators tend to work long shifts in physically and mentally draining work environments using heavyweight and cumbersome cleaning equipment – a combination that presents issues for good long-term workforce health and staff availability.
Because of the tasks they undertake, cleaning operators can suffer from work-related musculoskeletal disorders impacting the back, shoulders and neck. In 2018, the U.S. Bureau of Labor Statistics reported that more than 900,000 days away from work across U.S. businesses were due to employee struggles with the impact of muscular pain and injury, known as “ergonomic injuries.” The specific requirements of the cleaning sector, which asks operators to manually manipulate hefty loads and spend hours moving a range of cleaning machines, are among the primary factors driving operator overexertion and fatigue.
Such health-related challenges mean cleaning team managers must constantly battle workforce churn and elevated levels of staff absenteeism. The Bureau of Labor Statistics reported the national absence rate to be 3.1 percent in 2023, while Teamsense says that 5.4 percent of full-time U.S. employees were absent from the workplace due to a health-related issue in 2024.
The consequence of a taxing workplace environment could mean operators choosing to vote with their feet, by turning their back on the cleaning sector and seeking alternative employment elsewhere.
This is not a new problem. The people problem is long-standing and has been compromising workforce strength due to unplanned absences and staff shortages for some time, with cleaning roles cited as constantly exhibiting among the roles with the highest number of job openings. And it means facility management teams are faced with the challenge of continually altering shift patterns and potential delays to cleaning. This is not only a significant administrative burden, but it can also potentially lead to a failure to deliver contracts or meet service level agreements, and in some cases, financial penalties and long-term reputational damage.
To tackle the issue, a new concept for cleaning machine design is needed. One that puts people at its core and creates intuitive, adaptable, easy-to-maintain and ergonomically sound cleaning machines, which can deliver a multitude of people-first and operational benefits.
Adopting an ergonomics-first approach
FM teams encompass a range of people with unique needs, skill levels and work experience. Today’s cleaning machine solutions – which are often operated by multiple users – need to address these differences, adapting simply and effectively to individual user needs.
Modern cleaning machines should offer ergonomic flexibility, which will alleviate injury potential through manual adjustment to match individual operator characteristics, such as their height. This will ensure facility staff are less exposed to the typical muscle-related problems and fatigue that impact resource planning and retaining the cleaning operator levels needed.
Such machine development supports a better user experience, lessening the physical and mental strain of machine operation. It can also deliver practical operational efficiencies by incorporating a range of features designed to simplify machine operations for users and remove the traditional challenges they face.
Using design to simplify maintenance routines
FM operations will typically use a variety of cleaning machines, each often representing a significant level of investment. As a result, purchasers want the assurance that value-added machine performance is maximized for daily cleaning effectiveness. They also want to guarantee a high return on investment over the long term.
But in the real world, time pressures, a lack of training support, complicated maintenance processes and the need to “just get on with the job,” can potentially see routine maintenance requirements for cleaning machinery assets fall by the wayside.
According to research by IBM, strategic and proactive maintenance for machines, such as cleaning equipment, can reduce downtime by up to 50 percent, increase productivity by 20-50 percent, reduce breakdowns by 70-75 percent and cut maintenance costs by 5-10 percent.
The need for proactive maintenance is not a new concept. Cars or home boilers are two other examples in which the absence of maintenance and servicing will lead to inevitable outcomes such as compromised performance, costly repairs and even failure. Cleaning machines are no different, as they undertake repeatable cleaning cycles, often in tough operating environments.
It is well recognized that compromised or ineffective maintenance for cleaning machines impacts efficiencies, shortens machinery lifespans and introduces the potential for reputational damage linked to reduced quality cleaning outcomes.
But this can be addressed and simplified with a practical-based approach to new machine design and use. For example, design could incorporate:
-
A unique interface that can be tailored to the user’s language – meaning instructions and notifications can be easily understood and actioned without delay.
-
A tailored interface that represents the user’s skill level – for example, limiting the functionality offered to less experienced users to avoid confusion and ensure essential notifications are not overlooked.
-
Color-highlighted user touch points – so users can see easily where attach/detach functions lie for removing cleaning decks or topping up cleaning solutions when conducting essential maintenance, for example.
-
Easy-to-remove attachments, such as squeegees – ensuring these are quick and easy to attach, detach, clean and store.
-
Time-saving features – such as a water filling indicator, so users can easily keep this topped up to maximize clean quality, without having to repeatedly stop to check and refill.
-
On-machine training, delivered via a unique user interface – so users can check any operating questions simply, without delays to cleaning tasks.
Each of these developments simplifies the operation and maintenance of expensive machines, ensuring daily tasks to optimize performance are quick and undemanding for users.
Alongside these design innovations, there are also practical steps businesses can take to tackle the long-standing maintenance challenge, without putting additional pressure on cleaning staff.
These will support, and not disrupt, day-to-day cleaning operations, helping to maximize high-quality cleaning and enhance cost-efficiency and productivity:
-
Involve employees – while easy maintenance routines will optimize cleaning machinery performance, how the machines are operated can also have an impact on extending their lifespan. Working with cleaning staff to share the importance of user behavior is critical. This involves educating them on why routine maintenance is vital and sharing how simple this process can be.
-
Precalibrate for success – look for machine solutions that can be precalibrated to automate material use, speed and machine power. This can help alleviate the tendency to always select maximum settings, which could otherwise put unnecessary strain on the machine. This will also support sustainability and cost-efficiency objectives, as resource waste is reduced and the use of expensive materials optimized.
-
Automate proactive maintenance notifications – ensure equipment has the functionality to proactively notify users when maintenance tasks are due. This will help to keep up routine maintenance and support with long-term planning around machine availability.
Progress in cleaning machine designs is making things simpler for operators and FM teams. Based on a people-centric perspective, a new adaptable and ergonomic-first design approach addresses operator individuality, as well as skill and experience variances, to reduce physical and mental strain on cleaning teams. It also ensures critical machine maintenance obligations can be undertaken with ease, guaranteeing minimized asset downtime and optimal lifetime performance for cleaning equipment.
New levels of productivity, operator satisfaction, cost efficiencies and machine life cycle input are now within reach for facility cleaning teams – all without adding extra pressure to the user’s responsibilities.
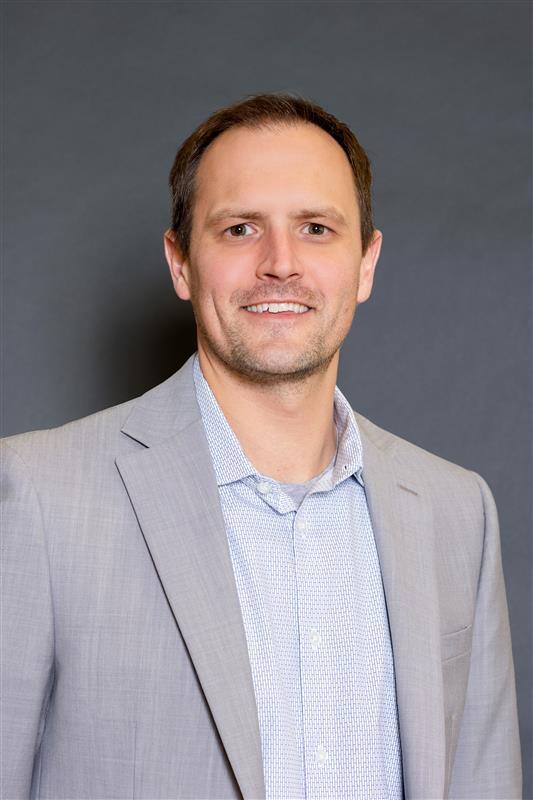
Rick Maday is the director of product management for the Americas at Nilfisk Inc. His primary responsibility and expertise is understanding the customers’ needs. Maday has spent more than 15 years crafting an ability to translate customer understanding into impactful solutions having worked for Pentair and Fluke Corp. prior to joining Nilfisk.
Read more on Occupancy & Human Factors , Real Estate and Operations & Maintenance
Explore All FMJ Topics