The Integration of Metasys with FMS:Workplace
When every minute counts, this innovation can save the day
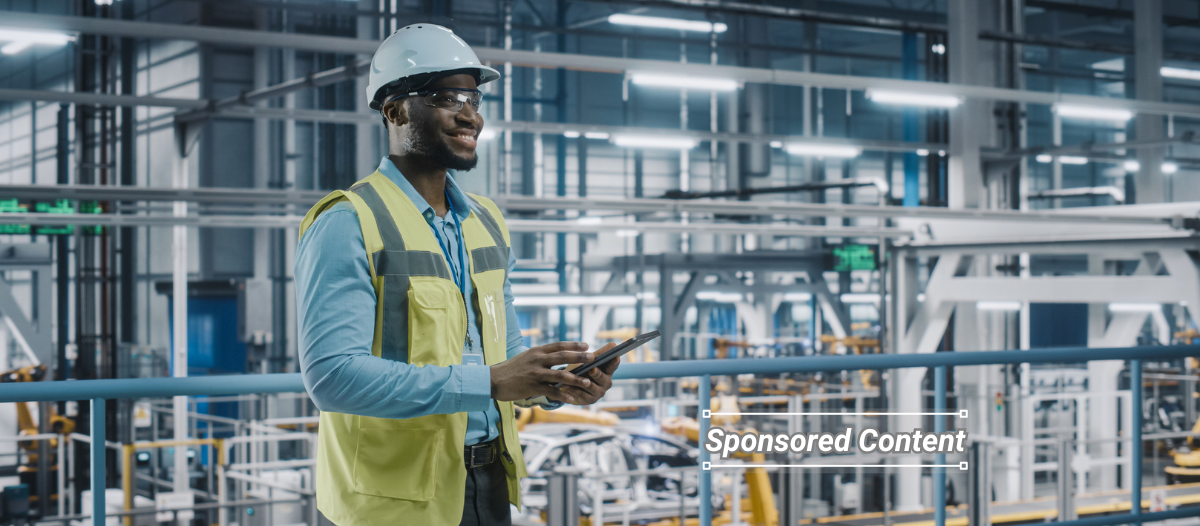
Identifying and addressing suboptimal performance in building equipment is a race against the clock. Left unresolved, small problems like a worn-out belt or bearing can end up causing damage to equipment, other building systems and even the facility itself. But without the help of facility maintenance technology, facility managers (FMs) might not be aware of an issue until building occupants start noticing its symptoms, like poor indoor air quality (IAQ) or excessive noise. By then, it could be too late to avoid costly repairs and disruption.
For over three decades, Johnson Controls Metasys building automation system (BAS) has provided FMs with early warning of potential problems by monitoring components around the clock. Metasys notifies FMs immediately if it detects anomalies, such as increased vibration or energy usage, in the operation of a piece of equipment. FMs receiving these alarms can then create a work order ticket and assign a technician to investigate the problem and carry out repairs.
Now, a new integration of Metasys into FM:Systems FMS:Workplace facility maintenance solution streamlines and automates this work order process, saving FM’s critical time in dealing with potential issues. The integration allows for a rapid response to equipment alarms by qualified technicians, minimizing wasted effort, improving maintenance resource utilization and enhancing tenant satisfaction.
Two pioneering solutions come together
Launched in 1990, the first generation of Metasys was a collection of hardware and software control components that worked together to automate the operation of a building’s HVAC, lighting, and other mechanical and electrical subsystems. That original iteration pioneered the use of a personal computer as an affordable BAS host, and the evolution of Metasys since then has been driven by advancements in technology, from the worldwide web to Internet-of-Things (IoT) sensors. Among other improvements, the latest version — Metasys 14.0 — is the first to feature a continual release model, enabling users to access new functionality as soon as it’s available rather than making them wait for roll-out of the next version.
FMS:Workplace is an integrated workplace management system (IWMS) with a pedigree that also dates back more than 30 years. Organizations utilize FMS:Workplace to manage, analyze and report on the operation and maintenance of their facilities. With FMS:Workplace, FMs can set up recurring schedules for equipment inspections and routine maintenance and easily assign those tasks to a technician. Access to accurate data means FMs can deliver better customer service, reduce costs and improve the performance of their facilities. A critical component of FMS:Workplace is the ability to integrate enterprise data from other departments, such as Human Resources and Accounting.
The integration of these two platforms consists of an application programming interface that automatically triggers the creation of a work order ticket in FMS:Workplace when an equipment alert is received in Metasys. Data mapping between the two systems ensures that the ticket, which is created in the FMS:Workplace Facility Maintenance Module, includes all the details required to efficiently address the issue. This reduces unnecessary trips and wasted time, while also decreasing the likelihood of errors from manual entry. The ticket is then dispatched to the most appropriate service center for technician assignment, taking into account the location and type of maintenance work needed. Once the technician completes the task or repair, information is sent back to Metasys to resolve and close the initial notification.
In addition to streamlining the corrective maintenance process by automating work order ticket creation, the integration of Metasys with FMS:Workplace helps FMs optimize their maintenance regimens and lay the groundwork for predictive maintenance (PdM).
It’s about time
It didn’t take long after humans started building structures for people to figure out that waiting for something to break wasn’t ideal. They learned quickly, for example, that replacing roof material on a regular basis reduced the occurrence of leaks. Today, technology like FMS:Workplace makes it possible for FMs to carry out that same kind of preventive maintenance (PM) on facilities that are much larger and more complex.
But even with the most robust technology and processes in place to support a PM program, issues will still pop up. That’s because traditional PM uses time intervals, rather than actual equipment usage, as an indicator of necessary maintenance. FMs who set those time intervals too short may be wasting time, effort and money on maintenance that’s not needed. On the other hand, scheduling too much time between inspections increases the risk of an equipment failure. The integration of Metasys with FMS:Workplace gives FMs an alternative to time interval-based PM by providing “run time” values for individual pieces of equipment.
The integrated system creates a powerful new workstream that empowers FMs to better understand actual equipment usage and make more strategic and informed maintenance decisions. By combining asset records with sensor data, FMs can develop a maintenance schedule based on actual asset health rather than trying to guess at an optimal time interval that walks the thin line between waste and costly equipment failures. In this way, it represents a bridge to PdM.
Delivering multifaceted benefits
Over the course of just a few hours, a small issue can become a big problem — for occupants, owners, landlords and, ultimately, FMs. Automating work order creation in FMS:Workplace can help cut the response time to an emergent issue from hours to minutes, eliminating wasted time and effort, decreasing greenhouse gas emissions, improving customer satisfaction and reducing costs.
Efficiency:
Every dam break starts with a tiny crack, and fixing the crack requires much less time, effort and money than dealing with the deluge. The integration of Metasys with FMS:Workplace allows FMs to address issues within minutes, while they’re still isolated and minor, instead of waiting until they’ve been allowed to impact occupants, other systems or the facility itself.
The integrated system also improves efficiency by ensuring that technicians have everything they need to resolve the issue, including asset, space and warranty information, as well as product documentation. This creates a higher-value engagement for the technician and enables them to close tickets faster. The system also reduces the need for inefficient manual processes by creating connective workflows.
Sustainability:
Greater efficiency translates into a smaller carbon footprint. Case in point: If a technician can resolve the problem in one trip rather than three on-site visits, that represents a 66 percent reduction in automobile emissions for that ticket.
Catching problems early and dealing with them efficiently also means it’s less likely the issue will require total asset replacement. The greenhouse gas emissions embodied in the manufacture and transportation of new equipment can add substantially to an organization’s carbon footprint. The portion of the old equipment that ends up in a landfill can also be a drag on progress toward sustainability goals.
Finally, suboptimal performance often results in equipment working harder and using more energy. Identifying and fixing these issues as soon as they pop up minimizes excess energy consumption and energy waste.
Customer satisfaction:
The top priority of any FM is to ensure the safety of, and minimize disruption to, building occupants. By taking much of the guesswork out of PM and providing an entrée to PdM, the integrated system decreases the chances of unanticipated downtime.
Even PM that’s scheduled far in advance can be disruptive to occupants, with the potential for loud noises and decreased asset availability. Eliminating unnecessary preventive maintenance keeps those disruptions to a minimum.
By providing FMs with more data and actionable insights into conditions, costs, performance and remaining useful life, the integrated system brings reduced asset failures and less downtime, while allowing FMs to provide customers with more complete and accurate projections for remediation when bigger issues do emerge.
Cost:
Being able to respond more quickly and effectively to potential equipment issues can save organizations a substantial amount of money. After all, replacing a belt or bearing is much cheaper than having to buy an entirely new piece of equipment. Being able to more quickly and effectively respond to issues increases the return on investment in assets and extends component and system life cycle by up to 25 percent.
When buy-or-repair decisions become more complex, having more complete information about the performance of equipment over time can help stakeholders make the right call. The FMS:Workplace and Metasys integration helps users make better-informed buy or repair decisions by consolidating maintenance history and other critical details in one centralized system.
Finally, using PdM to help ensure optimal equipment performance also reduces energy waste, which in turn saves the organization money. Improvements to HVAC/VRF system performance alone can reduce energy consumption — and costs — by up to 30 percent.
Ushering in GenAI
According to the FM:Systems 2025 Inside the Workplace survey of U.S. business leaders, 76 percent of organizations are planning to deploy generative artificial intelligence (GenAI) in the next year to assist with the operations and maintenance of workplaces. Almost half of business leader respondents said they’re planning to implement automation. The Metasys integration with FMS:Workplace paves the way for adoption of these advanced technologies by not only increasing the volume of relevant, real-time data being collected from building equipment, but making that data easier to access and more useful.
The integrated system sets organizations up for trending, strategy and predictive modeling Foundational data collection to support GenAI and automation initiatives. AI-powered workplace management solutions can be fed data from Metasys assets to create a centralized database. These systems can then use that data to learn and be more effective at streamlining processes and automating functions over time, delivering bigger improvements in efficiency, sustainability and cost reduction.
Conclusion: The many benefits of catching problems early
The failure of a large piece of equipment often starts with the most basic of parts. Catching suboptimal performance when it’s inexpensive and relatively easy to fix can bring a wide range of benefits, not the least of which is improved customer satisfaction and retention. The integration of Metasys with FMS:Workplace gives FMs another essential tool to shorten response times and address minor issues before they can become major ones.
By linking these two powerful platforms, Johnson Controls and FM:Systems are delivering a new level of building automation and preventive maintenance that ultimately empowers FMs to minimize costs, reduce disruptions, maximize uptime, and extend asset life.
Read more on
Explore All FMJ Topics