Are You Ready?
Taking control of water damage & IAQ events
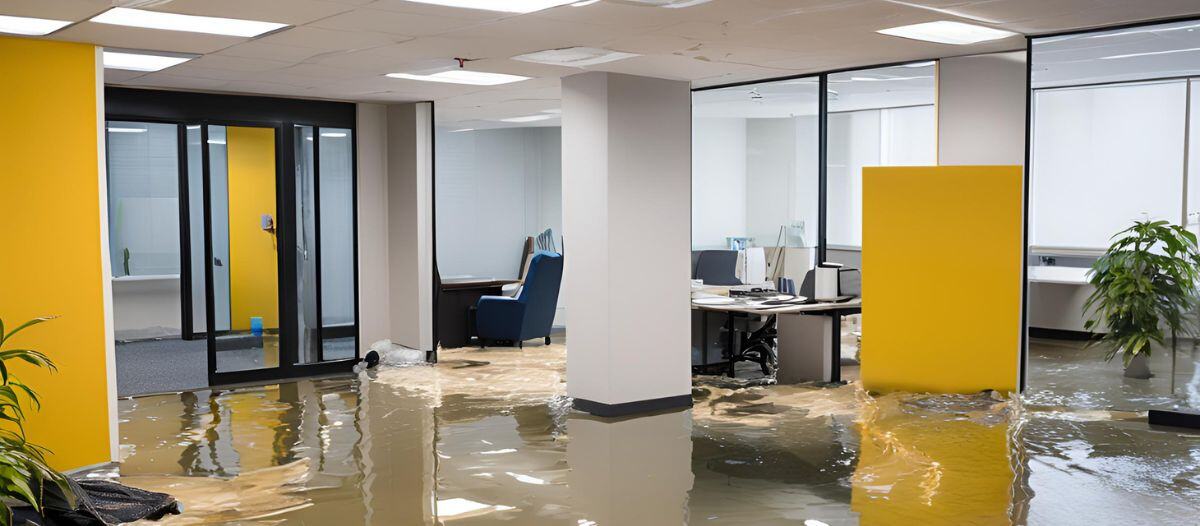
Flooding emergencies, air quality events, and weather-related problems are becoming more frequent and, in many cases, more extreme than ever before. Just this year, wildfires brought smoke and hazardous outdoor air quality to wide swaths of North America, and areas around the world experienced dangerous flooding from an increase in tropical storms.
Every day facilities face the threat of both large-scale emergencies and smaller, acute challenges like flooding from winter pipe freeze-ups, sink overflows and noxious fumes from maintenance and repair projects. Given rising insurance costs, true readiness for water damage and indoor air quality (IAQ) emergencies is critical to operational efficiency – and facility managers’ peace of mind – in any building environment.
But how do FMs go from total dependency on outside contractors to taking control of water and IAQ emergencies? By objectively assessing response protocols and filling the gaps, FM professionals are empowered with options – to either fully handling an emergency in-house or starting the process while waiting for contractor response.
Being ready to respond in-house can save 20 percent or more on mitigation costs, given today’s high insurance deductibles and contractor costs. With water damage restoration costs averaging $3-4 per square foot, a one-floor sprinkler activation can easily approach US$80,000 – so the potential savings is significant.
In addition to saving money, a facilities program that is fully ready enables an institution to return to business faster following an event, and helps maintain an overall environment of cleanliness, health, and safety. Having a standardized response program in place for handling these unwanted moisture and air quality events is a winning proposition for facilities planning, budgeting and operations.
Conversely, not establishing a first responder program can lead to dire consequences, including collateral damage like mold and mildew, lost business and health hazards for building occupants.
Guide for developing readiness
Merriam Webster defines readiness as “the quality or state of being ready, such as a state of preparation, prompt willingness, or ease/facility.” Being truly ready for an emergency means being prepared and having a step-by-step process defined, as well as establishing the culture and leadership to act with a sense of urgency and purpose.
In many cases, an organization can mobilize staff and equipment, but tactically lacks knowledge of the exact steps, science and technology. Gathering all the necessary data upfront prevents organizations from creating their own illusions of current outcomes.
A thorough assessment process, consisting of the following key components, is an important first step toward establishing response-readiness.
1. Initial assessment
Assess mitigation and restoration needs. Conduct a thorough, baseline assessment of the organization’s facilities that require cleaning or restoration plus equipment and materials available to determine the scope and resource requirements. The best way to get an objective, thorough initial assessment is through an onsite visit by an independent third party.
Proper assessment entails a full tour of facilities with key leadership present, including an inventory of response tools and equipment currently available. Some questions to be asked and answered during an initial assessment include:
- Who is expected respond to water damage or IAQ emergencies?
- Have all potential responders received training?
- Is all the equipment needed readily available?
- What is the exact process for responding?
A good assessment drills down to logistical details such as locating electrical outlets for powering equipment and checks to ensure that it works properly, air quality readings against EPA standards, and noting storage locations for each piece of equipment. Many organizations believe they have everything in place, while others know they need to start from scratch – and it is important to clearly identify the status and the most critical gaps.
2. Detailed protocols
Develop mitigation and restoration response protocols. Create detailed, step-by-step procedures for different tasks, including the use of specific cleaning agents, water damage restoration equipment and PPE. Procedures should cover precise roles and responsibilities for staff and incorporate cleaning and restoration industry best practices.
Many organizations that do this well use a flowchart that outlines the standard operation procedures in case of an emergency. For example, starting with:
- Step 1 – Locate the source of the intrusion and turn off water or stop the flow.
- Step 2 – Identify what type of water it is, whether clean water or black water (from river water or sewage).
- Further steps on specific procedures for selecting equipment, setup and disinfection.
In each case, the protocols must clearly outline what comes next: for example, Step 3 will differ in a clean water scenario, where in-house staff can start extraction and cleanup protocols immediately, versus Step 3 in a “dirtier” case where an outside contractor must be secured.
3. Employee training
Provide comprehensive training. Train FM staff on the standardized protocols, emphasizing critical timing, accuracy and consistency. FM staff benefit from first responder training to prepare for how to be the “coach” on game day when an emergency occurs, including how to:
- Properly set up and operate equipment
- Identify potential safety hazards
- Prevent mold and mildew
- Employ general best practices for healthy cleaning and restoration
Industry partners offer hands-on training where staff can literally get their hands, feet and pants wet while drying out a building space – using moisture meters and learning how to select and place drying and/or air ventilation equipment properly. Other video and hybrid training options are also available.
Beyond the FM staff, everyone who may be involved in response – essentially, all building occupants – can benefit from a 10-minute training that focuses on initial actions to take when an emergency occurs. Clearly outline safety concerns, such as potential electrical hazards in the case of water intrusions, as well as actions that must be taken immediately to halt a water source. Employers typically prepare building occupants on what to do in case of a tornado – go under the desk – and preparing for flooding or air quality events is just as important.
4. Equipment inventory
Use appropriate equipment and supplies. Ensure all necessary equipment and supplies, including tools, equipment, PPE and appropriate cleaning and disinfecting agents are on hand – and that equipment is checked and maintained regularly to ensure optimal functionality.
- What monitoring tools are available for moisture inspection?
- Are storage spaces for equipment adequate?
- What disinfectants are being used?
- What equipment is available for extraction, drying, dehumidifying and air filtration?
All fans are not created equal – drying out a water damage emergency requires commercial-grade equipment with the right technology, designed for that purpose. Cutting costs on equipment intended to handle flooding and IAQ emergencies can have serious consequences, including extended drying times that lead to worse damage later, blown fuses from overloading circuits and occupant health issues.
Similarly, when it comes to monitoring, moisture meters designed specifically for gauging water damage are easy for staff to use and will help save on costs and downtime. While facility staff often use the “touch test” to see if a carpet or wall is wet, it is not at all accurate for determining if materials are truly dry.
5. Documentation
Develop documentation and record-keeping. Establish a system for documenting cleaning and restoration activities, including schedules, tasks performed, tools used and outcomes.
Documentation helps track progress, identify areas for improvement and comply with safety and health regulations. When an insurance claim is filed, documentation is required for every detail, expense and procedure. In a public environment such as a university system, proper documentation is often necessary for institutional guidelines and capital planning.
Remember: water damage handled inadequately initially is a potential mold problem later. It is critical to track internally what worked and what did not in terms of equipment, logistics and staffing to see true improvements in outcome over the long term.
6. Quality control
Implement quality control measures. Regularly evaluate response program effectiveness through inspections and assessments. Collecting updated quality assessment data provides evidence of change from the baseline data and ensures a higher rate of success with each case.Organizations that complete routine assessment and implement quality control go from reactive to proactive, and from a focus on finding faults after the fact to a culture of forward thinking – providing tools for success before they are needed.
Quality control assessment incorporates gathering honest feedback from staff, customers and stakeholders to identify and address issues promptly:
- What worked and what did not?
- If it did not work, why not?
- Is this a systemic issue or unique to this emergency?
Most importantly, quality assurance comes from the outside – from a trusted, third-party source. Assessments can be clouded by having an insider’s perspective, so it is key to secure a partner to objectively assess what is truly happening.
7. New technology
Stay informed about emerging technologies and practices. Monitor advancements in mitigation and restoration technologies and practices and incorporate new techniques and tools to improve processes along the way. As with most industries, technology in the water damage and building restoration industry is constantly changing – and advancements bring a new level of efficiency and convenience to the job.
Consider the cleaning industry, where instead of an employee having to constantly check paper towel dispensers – today’s technology provides automatic alerts to indicate remotely when supply dwindles too low.
For FM professionals handling water losses in-house, gone are the days of having to physically visit multiple worksites every day to take moisture readings and ensure equipment remains plugged in and working properly. All this information is available digitally from virtually anywhere.
8. Communication
Communicate clearly internally. Establish clear communication channels to help relevant parties stay informed about response requirements, updates, and changes to protocol. Also, make training materials, inspection reports and corrective actions accessible to all team members.
Some organizations maintain a central communication system, which works well to ensure efficient response and eliminate duplication. For example, some organizations have a central phone number posted on signs throughout all buildings on campus. Any calls to that number go directly to the work order management team, where the job is then promptly assigned.
In establishing communication channels, remember that emergencies do not follow a regular work-week calendar. A sprinkler main can break on a holiday, a pipe freeze-up can occur during a school vacation week and a tropical storm can hit over a weekend. Work with staff to develop an on-call schedule so that off-hours events will be covered in a timely manner, averting further damage.
By following these steps, organizations can become truly ready to respond when an emergency event occurs. Having a clear strategic response plan in place ensures consistency and effectiveness in mitigation and restoration efforts, contributes to a healthier and safer environment overall, and saves time and costs.
Beyond the benefits to the organization and the facility, true readiness relieves worries and headaches for the FM and positions the team to be in control when inevitable water damage and IAQ emergencies occur.
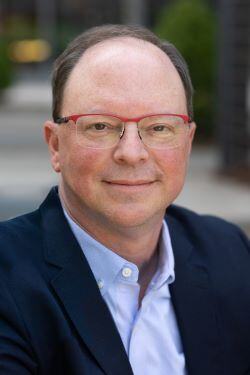
Tim Poskin is the MRO Program Director for Legend Brands, managing its Ready2Respond Facility Assessment Program. He serves as chair of the ISSA Cleaning Management Institute (CMI) Workloading and Benchmarking Council and is the former director of the ISSA Consulting Division. Poskin is one of the world’s leading authorities on cleaning and restoration workloading, converting outsourced response contractors to in-house response specialists and transitions from polluting programs to restoration systems.
Read more on Operations & Maintenance , Real Estate and Risk Management
Explore All FMJ Topics