Don’t Drop the Ball
How a CMMS can make or break an FM organization’s success
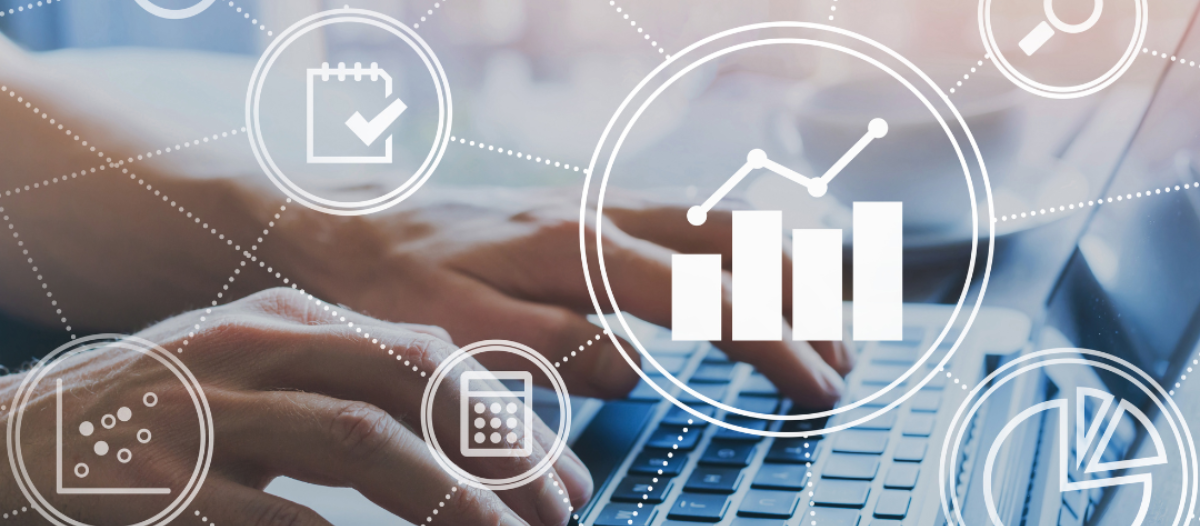
These systems are intended to provide FM staff with the data and reporting capabilities necessary for buildings to run smoothly and cost-effectively, and enable ease of access for end-users, including tenants, engineers and FMs. When working at peak performance, they also help eliminate surprises, uncertainties and frustrations. This is critical for keeping property managers, tenants and FM staff happy and boosting retention for the FM team. The problem is that many organizations implemented CMMS years ago — and their systems are no longer adequate for today’s demands.
For instance, some CMMSs require FM teams to spend a lot of time on manual data entry and number crunching, digging through data to glean actionable information. In addition, tracking work orders and preventive maintenance (PM) can be challenging, and communication capabilities limited — all of which hurts an FM’s team’s ability to deliver high-quality service.
FM leaders should evaluate whether their CMMS can meet current and future demands, decide whether to replace it and ensure their staff is following CMMS best practices.
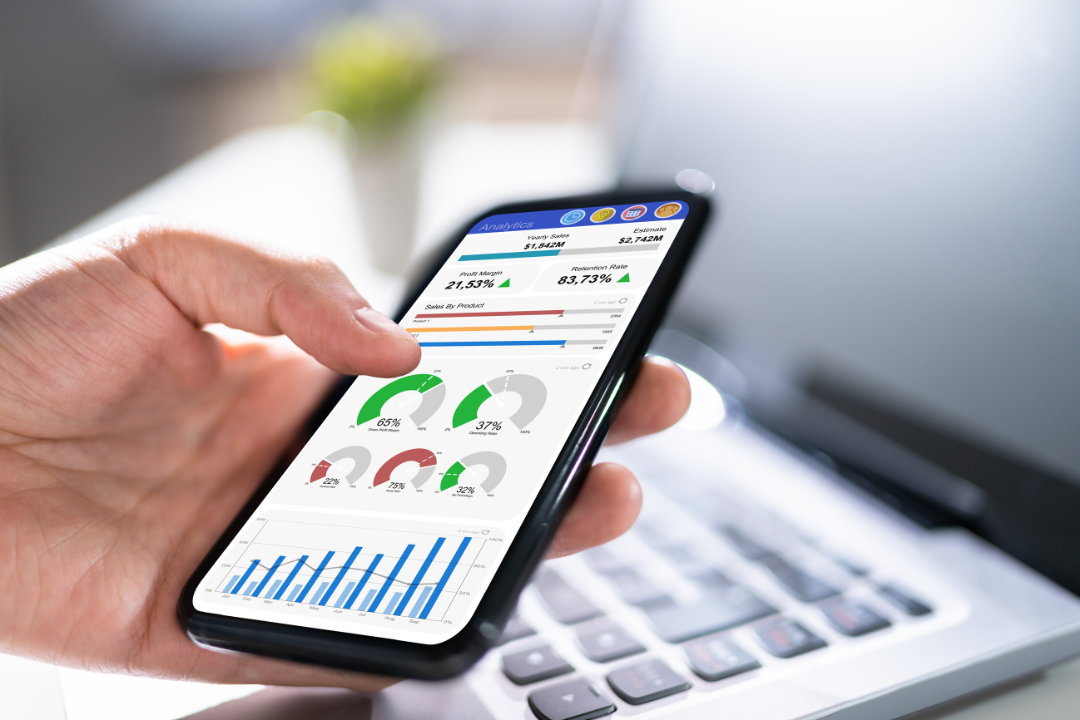
Evaluating an organization’s CMMS
Here are questions to consider when evaluating the efficacy of an existing CMMS.
-
How easy is it for CMMS operators and other stakeholders to use?
Does the CMMS enable access via mobile application, browser or tenant portal? Are the interfaces for all access points intuitive and well-functioning? Does the system enable sufficient information sharing and communications?
For instance, can FM workers access customized dashboards that show only their tasks? Can people easily attach photos and other documentation that help FM staff perform PM and reactive tasks?
Keep in mind that some facility engineers are not well-versed in navigating websites or accustomed to managing online accounts and passwords. If the CMMS does not have simple, clear interfaces and logons, FM staff may not use it correctly, or at all.
-
What types of reporting are available and are they intuitive?
The FM industry is increasingly data-driven. As organizations integrate more systems with their CMMS, such as building automation and enterprise resource planning (ERP), the volume and types of data available will continue to skyrocket. However, data on its own is not valuable if the right insights cannot be easily gleaned from it.
FM leaders should determine whether their existing CMMS offers the high-quality reports they need to gain insights and improve performance and outcomes.
-
Is a condition-based or time-based CMMS better for the organization?
Most sites today use time interval-based preventative maintenance. This means equipment is scheduled for maintenance based on time that has elapsed, regardless of whether the equipment has been consistently used and maintenance is needed.
These CMMSs work best when they are simple and do not try to tap into too many FM functions. They should focus on segments for equipment PM, equipment-based work orders, tenant space-based work orders and, as needed, guestroom/ apartment/conference/ball room preventative maintenance.
Condition-based systems, on the other hand, use sensors to track the equipment’s runtime hours and proactively alert engineers when PM is required. They also enable FM operators to enter customized parameters, such as seasonal maintenance for boilers (in the summer) and HVAC (in colder months).
If condition-based is preferred, does the facility have enough sensors onsite?
-
What method will optimize the organization’s operating costs long-term?
Although time-based systems can be costly in both labor and financial resources, sometimes they function well enough. For example, facilities can extrapolate data to demonstrate that a piece of equipment will have about 1,560 hours of run-time every six months because it operates from 0600--1800 Monday to Friday with no weekend run-time.
While condition-based CMMSs can save labor time and money in the long run, remember to consider all the costs of an upgrade, including sensors and integrations with the site’s existing building automation, ERP and other systems.
CMMS technology advancements
Modern CMMSs include capabilities that can help significantly improve preventive and reactive maintenance. Some even support the next level of predictive maintenance.
-
Cloud-based access: This enables easy access from anywhere with an internet connection.
-
User-friendly interfaces: Modern CMMSs prioritize intuitive user interfaces and user experience design. They are easier for maintenance technicians and managers to learn and use effectively. They also include enhanced communication features, such as chat. This improves interactions between FM staff and others who submit work orders.
-
Mobile accessibility: They often come with mobile apps or are mobile-responsive. This allows tenants and maintenance technicians to use cell phones and tablets to submit/access work orders and updates in the field and to receive real-time notifications on the go.
-
Integration capabilities: Newer CMMS can more easily integrate with building automation systems, Internet of Things (IoT) devices and sensors, and other enterprise systems such as ERP. This facilitates real-time data exchange, predictive maintenance insights and streamlined workflows.
-
Advanced reporting and analytics: Robust reporting and analytics provide wide-ranging insights into asset and personnel performance, maintenance trends, resource allocation and more.
-
Automation and AI: Some systems incorporate artificial intelligence (AI) and machine learning algorithms for predictive maintenance, anomaly detection and automated scheduling.
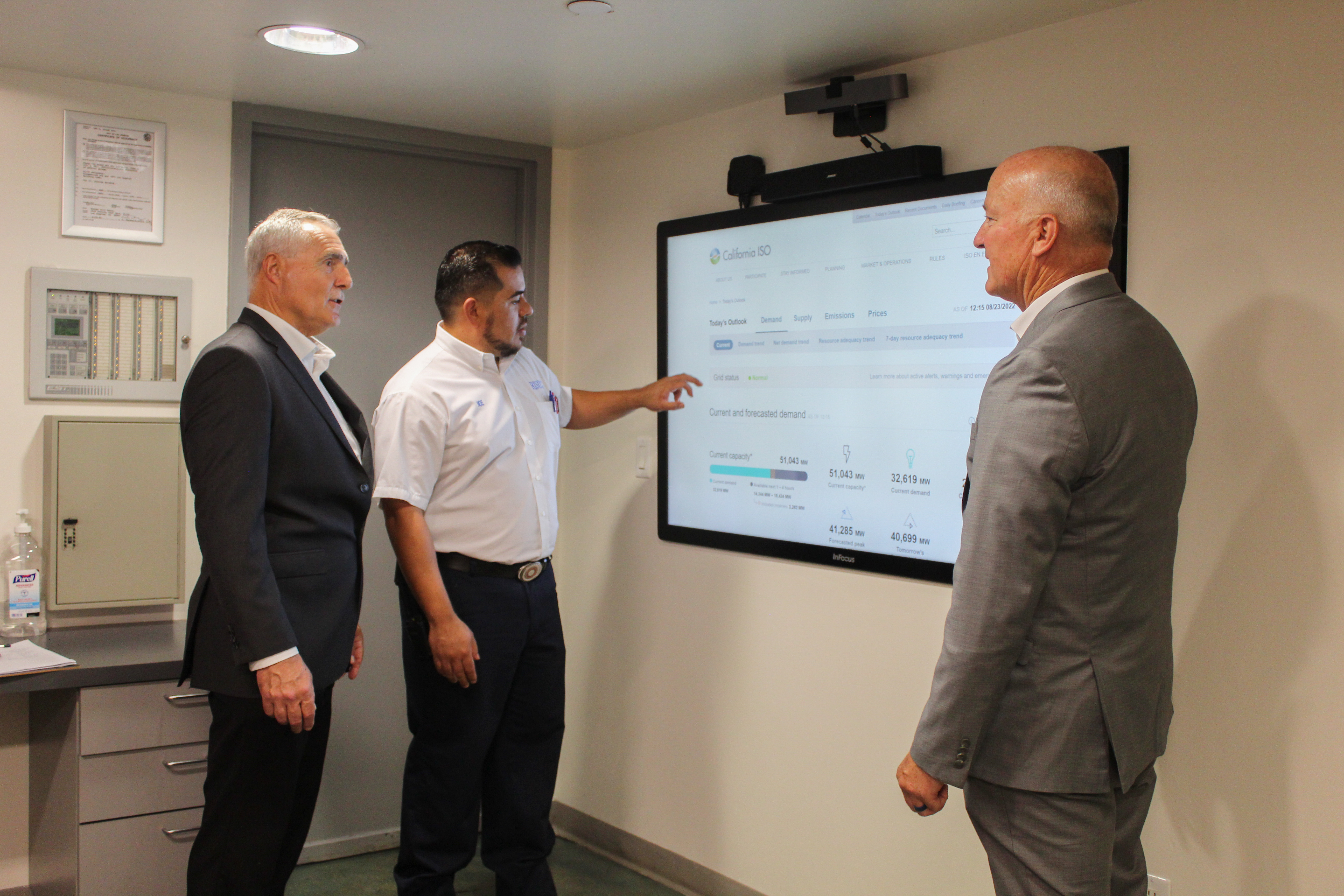
5 key benefits of high-quality CMMS implementations
When onsite technicians use CMMSs that are equipped with advanced functionality, the benefits have far-reaching impacts on facilities, teams and tenants:
-
Faster work order resolution
FM staff members can be notified as soon as statuses change on their assigned work requests. If stakeholders upload photos of the issue into the CMMS, it is also easier for technicians to understand the problem, troubleshoot in advance and quickly fix it.
-
Enhanced communications and customer satisfaction
Communications between the FM team that manages work requests, the employees and vendors who fulfill requests and the stakeholders who make requests, are all streamlined.
Time-stamped chats available in some CMMSs enable users to see who responded and when. As a result, tenant complaints and questions about work orders often drop dramatically, while customer satisfaction scores rise.
-
Simplified preventative maintenance, reduced downtime and lower costs
With PM streamlined and enriched with robust information and insights, organizations can better understand equipment life cycles and improve equipment longevity.
-
Staff planning and allocation
FM engineers can see how many tasks are assigned specifically to them and their priority levels. This helps them better allocate their time. The CMMS also helps managers determine whether more staff are needed, for instance, to resolve a particular work order or handle a scheduled PM.
-
Instant reporting and better decision-making
With the wide-ranging, intuitive reporting and rich FM-related data of a CMMS, organizations can instantly run reports showing everything from service legal agreement performance and individual technician productivity to types of comfort calls received, and hours spent repairing assets that are nearing end-of-life. These reports and more enable FM leaders to make decisions that save money, improve capital planning and productivity and delight their community.
Best practices for successful CMMS implementations
Regardless of whether FM organizations decide to keep their existing CMMS or upgrade to a newer one, it is important to follow these best practices:
-
Set it up right the first time. Be detailed and thorough. Take time to input all tenant information and all integrations with other systems and ensure every piece of equipment is uploaded correctly. If any mistakes are found, fix them right away.
-
Keep an up-to-date equipment list. Include all equipment for administrative functions and maintenance for electrical, fire life safety, grounds, HVAC, plumbing, safety and, as needed, guestrooms or apartments, conference rooms or other spaces. As equipment changes and fails over time, instantly update the list.
-
Upload all applicable equipment manuals, if possible. This can be completed after the initial setup. Add as much information as possible so field employees can easily access and benefit from it.
-
Complete training. Many operators do not have sufficient time in the workplace to train on the tools they use regularly, including multi-faceted ones like CMMS. Make sure to set aside time for focused CMMS training.
-
Transition data. If the decision is made to upgrade to a more modern CMMS, make sure to run all equipment and work order histories, as well as tenant information, and store the data in a remote drive that everyone can access. This will help ensure a smooth, issue-free transition.
FM organizations rely on CMMSs to help ensure that actions are taken to extend the life of onsite assets, and that tenant/guest work requests are completed promptly. When a facility’s CMMS requires too much manual effort or is challenging to use, it naturally results in delays, errors and higher costs.
Leaders need to make sure that their CMMS is up to par for today’s and tomorrow’s needs, that stakeholders can effectively use them and that any transitions are well-planned, cost-effective and occur without any service disruptions.
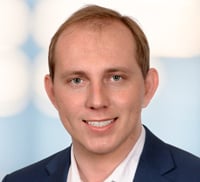
Michael Carmean, UG2 engineering manager, has strong expertise in computer maintenance management systems. He is well-versed in implementing strategic solutions for conducting asset inventory, developing tasks and maintaining preventative maintenance records, frequencies and compliance of all services. Prior to joining UG2 as engineering manager, he worked as an assistant engineering manager at a national service provider. Carmean earned his bachelor of science degree in engineering from California Maritime Academy. Upon becoming a certified journeyman engineer, he received his master’s in engineering management from the University of California, Los Angeles.
Read more on Operations & Maintenance , Project Management and Technology
Explore All FMJ Topics