Autonomy
The path to workplace safety
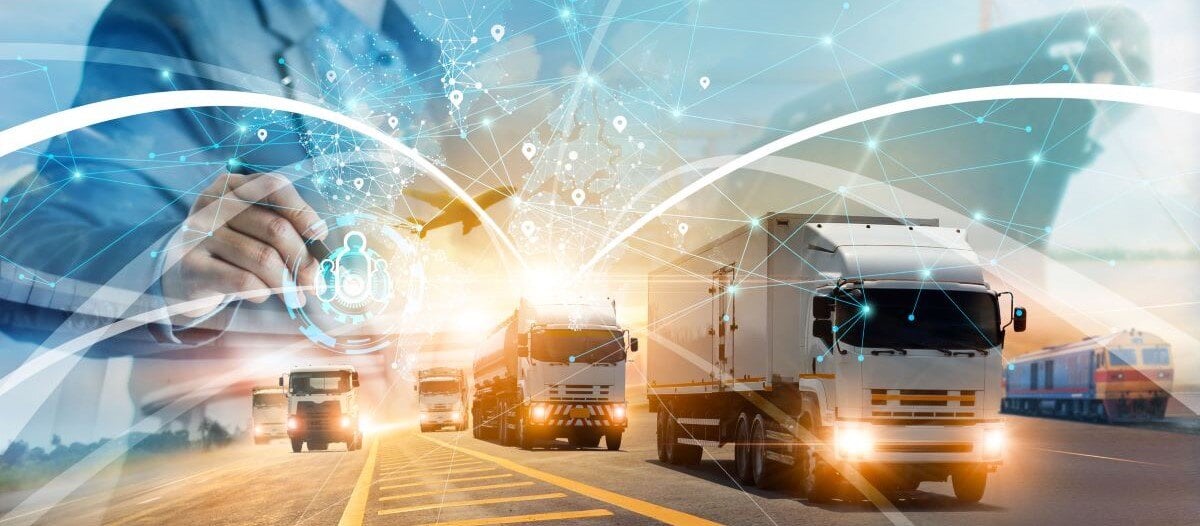
Equipment damage. Workers’ compensation claims. Occupational hazard insurance. All of these make up hefty price tags for employers in the event of workplace accidents or injuries, sometimes to the tune of billions of dollars per year.
This is especially true in logistics and transportation. Employees in this field are regularly tasked with physically demanding responsibilities, often set in hazardous environments. Distribution yards are one example. On any given day yard workers must navigate around 80,000-pound industrial vehicles and perform manual, repetitive and dangerous tasks in all kinds of weather. While many workplace accidents are just that – accidents – employers have a responsibility to do everything in their power to prevent such incidents from occurring.
According to OSHA, there were more than 1.3 million workplace injuries in 2023. Zoom in on the logistics industry: the 2020 injury rate in the warehousing and storage sector alone (4.8 for every 100 workers) was so concerning that OSHA launched a five-year initiative in certain states to reduce that number.
Transportation and logistics workers need solutions that enhance their safety on the job. Employers are responding by rolling out innovations in robotics and automation to lessen or eliminate safety risks. Autonomous distribution yard operations is one area redefining facilities operations for the better.
A closer look at the distribution yard
Distribution yards are an essential link in the supply chain that often go unnoticed. The transition point between warehouses and over-the-road trucking, distribution yards process about 20 billion tons of freight every year. Everything people eat, use and wear in everyday life passes through these yards.
But distribution yards are chaotic and congested places to work. Over-the-road trucks deliver and pick up freight. Yard truck drivers move trailers and containers on chassis around the property to parking spots and loading docks. Other traffic includes pick-up trucks, golf carts and delivery trucks (to name a few). Add in pedestrian traffic like maintenance technicians, warehouse personnel and logistics coordinators, and there is an exceedingly complex environment that requires meticulous attention to the safety of employees and equipment alike.
In addition to maneuvering around enormous industrial vehicles, employees are often exposed to hazardous emissions and particles like diesel exhaust, packaging and trash. The supply chain does not stop for inclement weather, which means workers perform already-dangerous tasks in harsh conditions.
With so many moving parts, accidents are bound to happen. As a result, logistics-dependent enterprises spend as much as US$1 billion in insurance claims costs for yard and loading dock accidents every year. However, the frequency and severity of incidents can be reduced by investing in zero-emission autonomous solutions built specifically for the unique needs of the distribution yard.
Enter: autonomous yard operations
The typical yard truck makes 6-12 trailer moves per hour in the yard. Over the course of 24 hours, a single vehicle completes upwards of 280 moves. For a human driver, that is between 48 and 96 moves in a single shift. This is manual and repetitive – and unlikely the best use of the driver’s skills. Add the challenge of negotiating around other vehicles and pedestrians, and the job becomes both draining and hazardous.
Distribution yards are ideal for autonomy not only because of repetitive, manual tasks, but also due to their location on private, well-defined property. However, autonomous systems must be able to operate in a complex, chaotic environment. Autonomous vehicles (AVs) with advanced perception capabilities can move with extreme precision, identifying obstacles in their path, yielding to oncoming traffic, and obeying yard traffic rules like stop signs and speed limits.
AVs can couple to and from trailers, which includes hitching and connecting the brake line. To move trailers between dock doors and parking spots, AVs must connect to trailers via pressurized brake lines. Human drivers complete this task, and it involves releasing the parking brake to move the trailer around the yard. It is a manual and dangerous duty that requires drivers to get in and out of their cab about six billion times per year worldwide, exposing them to the elements, harmful emissions, other vehicles and ergonomic issues.
AVs equipped with a robotic arm to connect and disconnect brake lines reduce the need for drivers to exit their vehicles. Robotic arms programmed to imitate human motor skills can easily take ownership of connecting truck to trailer, allowing drivers to remain safely inside their cabs.
To move trailers in distribution yards, AVs must be able to complete articulated backing, align to dock doors with centimeter accuracy and maneuver around obstacles. AVs use multiple sensors to continuously monitor obstacles in their path. Should the AV encounter an obstacle, it will automatically apply the brake and/or adjust steering. Equipped with hazard avoidance, the AV will keep a significant buffer between itself and surrounding objects. To make matters even safer, the right solution will be programmed to ensure its speed is the same as or less than the posted speed limit in the yard.
Additional benefits of autonomy
The movement of trailers and chassis around the yard is only one of many benefits autonomy stands to introduce to the yard. Other examples include:
- Cleaner, greener operations: By investing in autonomous vehicles designed with the future of sustainable yard operations in mind, supply chain leaders can cut down on employee exposure to harmful emissions. The best autonomous solutions will be electric, releasing zero emissions to positively impact the planet and yard workers.
- Streamlined trailer location tracking: When autonomous trucks are equipped with trailer inventory technology, the need for manually pinpointing the location of each trailer becomes obsolete. With sophisticated sensors and computer vision algorithms enabled by deep learning, AVs capture trailer identification numbers and standard carrier alpha codes, as well as confirm whether parking spots are vacant or occupied. This further minimizes the amount of traffic in the yard.
- Seamless integration into existing operations: AVs must be supported by the right management software. Dispatchers need the ability to manage AVs in the yard while retaining their existing workflows. The right solution will integrate with users’ yard or warehouse management software to centrally manage manual and autonomous yard trucks. Having an integrated solution gives dispatchers visibility into AV operations, including move status, move completion confirmation and trailer inventory. The right solution will also provide configuration and fine-tuned management of single, multiple or even fleets of autonomous yard trucks.
Reallocating human capital
It is critical to note that autonomy should not be considered a replacement for human labor. No matter how well-programmed or intricately designed, autonomous solutions cannot replicate the creativity and critical thinking skills humans possess.
Consider the advent of the robotic vacuum as an example. These household helpers are not capable of fully replacing human attention to detail. They struggle with tight corners and cannot go up or down stairs, and they often have difficulty getting over thresholds and under furniture. But they save an inordinate amount of time spent cleaning homes – so much so that dusting and vacuuming hard-to-reach areas becomes less of a burden. Such technology takes care of the repetitive task of vacuuming rugs and hardwood floors, so people can focus on using fine motor skills to tackle more complicated responsibilities.
Supply chain leaders should encourage one another to view autonomy as a means to enhance operations and free up human workers to focus on more valuable tasks better suited to their abilities and working environment. Coupled with the creation of new types of jobs and training programs to support AVs, deploying yard automation enables employees to do safer, more human-friendly jobs.
Building a safety culture
As yards become increasingly automated, employees can shift into less dangerous working conditions. But that does not mean safety should become any less of a concern. With autonomous solutions keeping the yard running smoothly, employees can reinvest their time building and upholding a strong culture of safety in their workplace.
Safety should be a continuous and concerted group effort. There are always forces at play that no amount of automation or technological development can correct for, like weather, gravity and inertia. By recognizing the impact of these forces on the distribution yard environment, supply chain leaders can arm their employees with best practices.
Ample training should always accompany the implementation of new technology, and autonomous solutions are no exception. Employees must learn how to properly interact with automated systems so they can use the technology to their greatest advantage. They need to be confident in their ability to:
- Identify AVs in the yard
- Understand when AVs are operating manually versus autonomously
- Recognize when it is safe to approach an AV
- Know how AVs interact/work with their dock doors
When distribution yards are enabled with autonomous solutions, employees are empowered to focus more of their energy on higher-value tasks. This reduces safety risks for both human workers and equipment; but introducing autonomy must be accompanied by safety training. Autonomy contributes to establishing a culture of safety, but it is by no means a replacement for human labor or critical thinking.
With a holistic approach to safety, facility leaders of logistics centers and hubs can demonstrate their commitment to employee well-being while simultaneously improving operations.
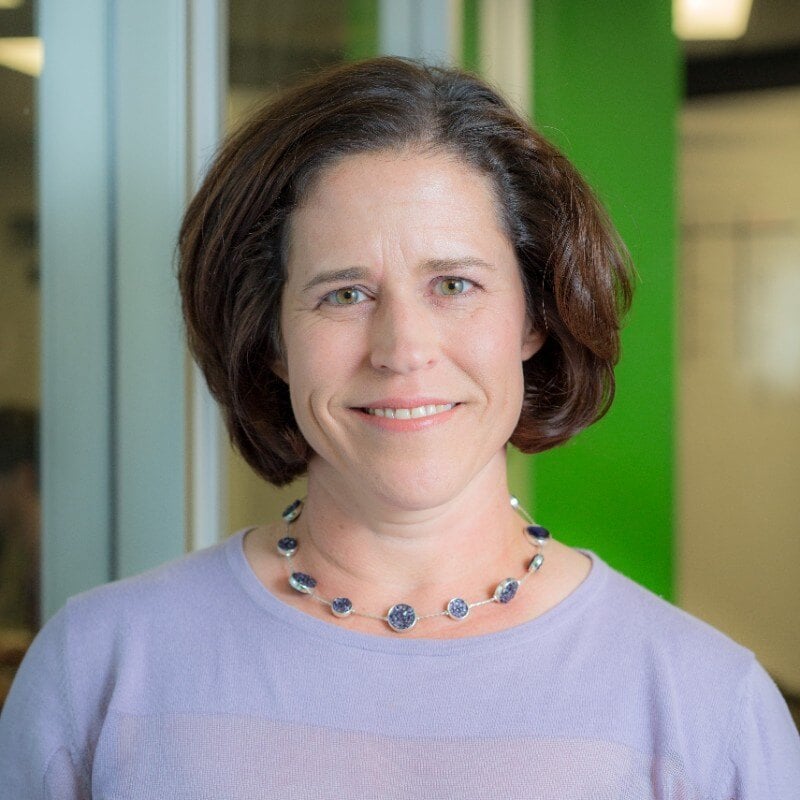
Londonne Corder is the chief marketing officer at Outrider. She is responsible for creating the yard automation industry category and building Outrider’s leadership in the market. Corder is passionate about working with Fortune 500 enterprises to automate their business operations to reduce costs and improve efficiency. With nearly 25 years of experience in high-tech hardware, software and SaaS, Corder uses outcomes-based marketing strategies across all aspects of the marketing mix, including corporate marketing, product marketing, customer engagement, demand generation, public and analyst relations, social media and operations. She holds a Bachelor of Science degree with high honors from the University of Kansas William Allen White School of Journalism.
Read more on Operations & Maintenance , Project Management and Risk Management
Explore All FMJ Topics