Going Up?
Keeping elevators safe & compliant
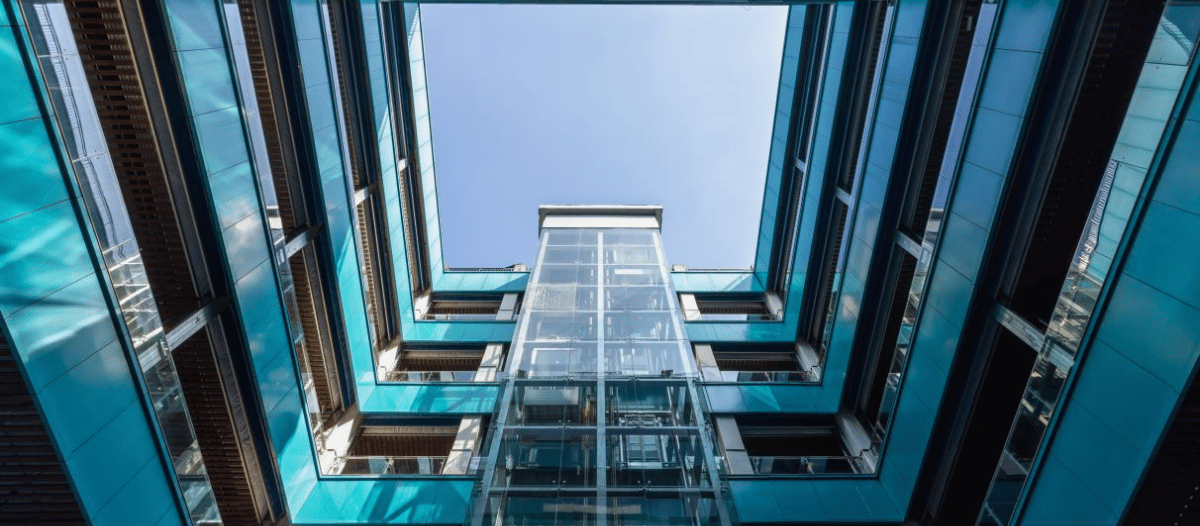
Understanding elevator codes
While elevator codes do not change often, when updates occur, they can have major implications for equipment, budgets and safety processes that FMs must be prepared for. These codes can vary greatly depending on the state and municipality, so FMs must research requirements for their specific location. Typical code requirements involve maximum elevator weight limits, emergency communications systems and door sensors, among others.
But additional upgrades above and beyond code may be advisable as well. When a major code changes, companies and buildings must engage with an elevator contractor to bring equipment up to spec. While budgeting for the minimum necessary upgrades to meet new codes is crucial, managers may find value in going further. Creating checklists of code requirements and timelines helps to plan and budget appropriately for all upgrades under consideration.
Some typical elevator code requirements include:
- Weight limits - Maximum capacity for elevator car and components
- Emergency communications - Phones or intercoms in elevators for emergency contact
- Door sensors - Devices to prevent doors closing on objects or people
- Door timing - doors open speed, time to remain open before closing, and close speed
Working with inspectors
Though elevator inspectors provide crucial and mandatory oversight, FMs must contract with regulators to enable unobstructed assessments while also keeping the riding public and their staff safe and ensuring that operations run smoothly.
Inspections vary in complexity and range from annual no-load checks to more rigorous five-year exams involving test weights, safety device checks and more. FMs should understand inspection protocols and coordinate with their service provider to have all documentation ready as well as providing access to machine rooms and equipment. While inspectors have authority to conduct tests, managers must also be mindful of the safety of all parties involved in the inspections.
The inspection process involves visual checks, testing functionality of components like doors and controls, and observation of test runs with and without loading. Tests focus on ensuring proper operation as well as compliance with safety and codes. Proper planning helps make inspections proceed efficiently while protecting inspectors and facility staff.
Prompt and transparent communication with inspectors will foster a collaborative environment conducive to addressing any issues or concerns promptly. FMs can leverage these interactions as opportunities to seek clarification on regulatory requirements, solicit feedback on maintenance practices and gain insights into emerging trends and best practices in elevator safety. By cultivating positive relationships with inspectors, managers can streamline the inspection process, minimize disruptions to operations and demonstrate a commitment to maintaining the highest standards of safety and compliance within their facilities.
Accessibility considerations
Facilities open to the public must ensure their elevators meet accessibility standards such as the Americans with Disabilities Act (ADA) which contains requirements covering all aspects of an elevator – location and access, size and space, controls and communication, door timing and safety, as well as signage. The goal is to make elevators usable for all people. Incorporating advanced accessibility features into elevator design enhances usability and reflects a commitment to social responsibility and customer satisfaction.
A proactive approach not only enhances the overall user experience but also strengthens the reputation and appeal of the facility within the community. Enhanced accessibility also benefits many others: Wider doors and additional time for entry assists parents with strollers or travelers with luggage, clear signage and safety sensors improve convenience for all. Standards, such as those outlined by the ADA, are the mandated minimum, but viewing upgrades through the lens of universal design means more users reap the benefits. Staying ahead of evolving codes future-proofs buildings for optimal safety and ease of use.
Emergency preparedness and response plans
In addition to maintaining compliance with regulatory codes and conducting routine inspections, FMs must prioritize the development of comprehensive emergency preparedness and response plans tailored specifically to elevator-related incidents. While elevators are typically a very safe mode of transportation, unforeseen emergencies such as power outages or mechanical malfunctions can occur, requiring swift and effective action to ensure the safety of passengers.
Comprehensive emergency plans should address building tenants and guests, emergency responders, elevator service providers and any other relevant stakeholders. Establishing clear protocols and procedures will guide occupants and staff on how to respond calmly and efficiently in the event of an elevator-related emergency.
One essential component of these plans is the establishment of communication channels to facilitate rapid notification and coordination during emergencies. This may include deploying emergency call systems within elevator cars, ensuring direct lines of communication with emergency services, and implementing protocols for communicating updates and instructions to occupants trapped in elevators.
Additionally, FMs should coordinate with elevator service providers to establish protocols for swift response and rescue operations. This may involve maintaining updated contact information for service technicians, establishing procedures for remote monitoring of elevator systems, and conducting regular training exercises to simulate emergency scenarios and test response capabilities.
Emergency preparedness plans should also outline evacuation procedures for occupants in the event of prolonged entrapments or situations where rescue operations may be delayed. FMs should work closely with building tenants and guests to designate evacuation routes, assembly points and alternative exits in accordance with established safety protocols.
Elevators require vigilant management by facility teams to maintain safety, meet codes, provide access and pass inspections. Keeping up with evolving regulatory standards, planning for necessary upgrades, budgeting properly and working smoothly with inspectors are key aspects of managing a complex facility. Documenting maintenance protocols, understanding inspection procedures and focusing on accessibility also optimizes elevator functionality. By making elevators a priority, FMs can significantly mitigate one of the highest-risk systems under their responsibility. A proactive approach helps elevators remain a safe, compliant and usable feature of the building environment.
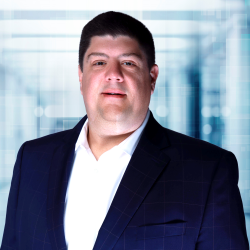
Dave Myers is the vice president of employee safety and health at American Elevator Group, a role he has held since March 2023. With more than 15 years of experience in employee safety and health, Dave has built a reputation for his leadership and expertise in environmental health and safety (EH&S). Prior to joining American Elevator Group, Dave spent a decade at Otis Elevator Co., where he advanced from Regional EH&S Manager to EH&S Associate Director. Earlier in his career, he worked at Pratt & Whitney as a Senior EH&S Generalist from 2006 to 2013.
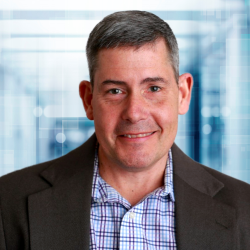
Doug Taylor is the vice president of quality at American Elevator Group, bringing more than 25 years of experience in the elevator industry. His previous roles include serving as director of quality assurance at Otis, where he honed his expertise in quality management and continuous improvement. A data-driven quality expert, Taylor is known for his ability to collaborate across functions, using continuous improvement tools to resolve technical issues and enhance product reliability throughout the lifecycle. His analytical approach focuses on reducing the cost of poor quality and strengthening overall business performance.
Read more on Operations & Maintenance , Project Management and Risk Management
Explore All FMJ Topics