Predictive Maintenance
Transforming FM with AI
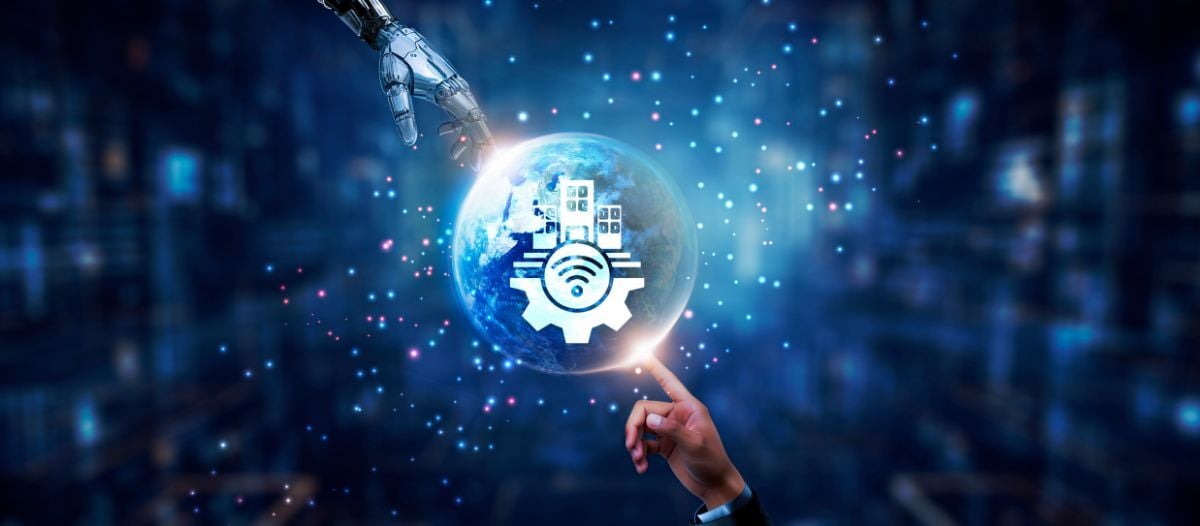
Facility management is undergoing a significant transformation, driven by advances in artificial intelligence (AI) and the Internet of Things (IoT). Predictive maintenance is at the forefront of this change, enabling FMs to anticipate and address equipment failures before they occur. By leveraging real-time sensor data and AI-driven analytics, predictive maintenance minimizes downtime, extends asset lifespans and optimizes maintenance costs. This proactive approach shifts maintenance strategies from reactive or scheduled servicing to a more intelligent, data-driven model, enhancing efficiency and sustainability across facilities.
How predictive maintenance works
Predictive maintenance utilizes IoT-connected sensors embedded in equipment to continuously monitor performance metrics such as temperature, vibration, pressure, electrical consumption and humidity levels. AI algorithms analyze this data in real time, detecting anomalies and predicting potential failures before they disrupt operations. When an irregular pattern is identified, the system triggers an alert, allowing maintenance teams to take corrective action before a breakdown occurs.
Key steps in predictive maintenance
-
Data collection: Sensors installed on machinery gather critical data such as vibration frequencies, temperature changes and energy consumption.
-
Data transmission: The collected data is transmitted to cloud-based AI platforms for real-time analysis.
-
AI analysis: Machine learning algorithms identify patterns, deviations and failure trends by comparing real-time data with historical performance records.
-
Predictive alerts: AI-driven insights generate alerts when equipment conditions indicate a potential failure.
-
Proactive maintenance: FMs and maintenance teams receive actionable insights, allowing them to schedule maintenance at optimal times, avoiding costly breakdowns.
Key benefits of predictive maintenance
-
Minimized downtime
Unexpected equipment failures can cause significant operational disruptions. Predictive maintenance prevents these issues by detecting potential malfunctions early, ensuring that equipment remains functional and reducing downtime.
-
Extended equipment lifespan
By addressing minor issues before they escalate into major failures, predictive maintenance reduces wear and tear, ultimately increasing the longevity of assets. This approach helps FMs maximize the return on investment (ROI) for expensive equipment.
-
Optimized maintenance costs
Traditional preventive maintenance often involves unnecessary servicing, increasing labor and material costs. Predictive maintenance ensures maintenance occurs only when necessary, reducing expenses related to unneeded inspections and repairs.
-
Improved energy efficiency
Faulty equipment often consumes excessive energy, leading to higher operational costs. Predictive maintenance ensures that machines function efficiently, reducing energy waste and lowering utility bills.
-
Enhanced safety & compliance
Equipment failures can pose serious safety hazards and regulatory violations. Predictive maintenance minimizes risks by ensuring machinery operates within safe parameters, supporting compliance with industry standards and legal requirements.
Real-world applications of predictive maintenance
-
HVAC systems in commercial buildings
Heating, ventilation and air conditioning (HVAC) systems are critical for commercial facilities. Unexpected HVAC failures can lead to discomfort, increased energy consumption and costly repairs. Predictive maintenance solutions analyze airflow, temperature fluctuations and compressor performance to identify issues before they escalate.
Example: A commercial office building implemented IBM Maximo for predictive maintenance on its HVAC systems. By analyzing sensor data, the system identified deteriorating performance in a chiller unit, allowing the maintenance team to replace a failing component before it led to system-wide failure. This intervention saved the company an estimated US$50,000 in potential downtime and emergency repairs.
-
Elevators & escalators in high-rise buildings
Elevators and escalators are essential in high-traffic buildings such as shopping malls and corporate towers. Predictive maintenance systems monitor motor efficiency, cable tension and door operation, preventing costly and dangerous malfunctions.
Example: A large hotel chain implemented SAP Predictive Maintenance across its properties, reducing elevator failures by 30 percent. AI analyzed door opening and closing speeds, detecting early signs of motor wear. Maintenance teams intervened before breakdowns occurred, improving guest satisfaction and safety.
-
Manufacturing plants & industrial equipment
Factories rely on industrial machinery for production. Unplanned downtime can result in significant financial losses. Predictive maintenance ensures that machinery remains in optimal condition, reducing downtime and enhancing production efficiency.
Example: A car manufacturing plant in Germany utilized Azure AI to monitor robotic assembly arms. AI models detected a slight increase in vibration levels, indicating a potential motor failure. By addressing the issue early, the plant avoided a two-day shutdown, saving approximately US$500,000 in lost production time.
-
Data centers & IT infrastructure
Data centers house critical IT infrastructure that must operate continuously. AI-driven predictive maintenance solutions monitor server temperatures, power supply fluctuations and cooling system performance to prevent downtime.
Example: A leading cloud service provider used IBM Maximo to analyze cooling fan performance in its data centers. The system detected anomalies in airflow patterns, prompting early fan replacement and preventing overheating issues that could have caused widespread service disruptions.
Leading predictive maintenance tools
FMs have access to several advanced AI-driven platforms to implement predictive maintenance effectively.
-
IBM Maximo: Utilizes AI and IoT to detect anomalies, manage asset performance and streamline maintenance workflows.
-
SAP Predictive Maintenance: Provides real-time equipment monitoring and predictive insights to reduce operational risks.
-
Azure AI: Leverages cloud-based machine learning to analyze sensor data and predict failures with high accuracy.
Challenges in implementing predictive maintenance
While predictive maintenance offers numerous benefits, its adoption comes with challenges:
-
High initial investment
Implementing predictive maintenance requires investing in IoT sensors, AI analytics platforms and system integration. However, the long-term cost savings and efficiency gains outweigh the initial costs.
-
Data quality & management
AI-driven predictive maintenance depends on high-quality, consistent data. Poor sensor placement, inaccurate data collection or insufficient historical records can limit its effectiveness. Regular calibration and data validation are essential.
-
Integration with existing systems
FMs often rely on legacy systems for maintenance operations. Integrating predictive maintenance solutions with these systems can be complex and require specialized expertise. Cloud-based AI solutions can help streamline this process.
-
Workforce training & adoption
Successful implementation of predictive maintenance requires training maintenance teams to interpret AI-generated insights and act accordingly. Organizations must invest in skill development and change management initiatives.
Future trends in predictive maintenance
As AI and IoT technologies continue to evolve, predictive maintenance is expected to become even more sophisticated and accessible. Emerging trends include:
-
AI-powered digital twins: Digital twin technology creates virtual replicas of physical assets, allowing real-time monitoring and predictive analysis.
-
5G-enabled maintenance solutions: Faster data transmission with 5G networks will enhance real-time monitoring capabilities.
-
Autonomous maintenance drones: Drones equipped with AI and thermal imaging will inspect large facilities for early signs of equipment wear.
-
Edge AI for on-site analysis: Edge computing will enable AI-driven predictive maintenance to analyze data on site without relying on cloud connectivity.
Conclusion
Predictive maintenance is revolutionizing FM by leveraging AI and IoT to prevent equipment failures before they happen. From HVAC systems and elevators to manufacturing plants and data centers, predictive maintenance offers unparalleled benefits, including cost savings, increased reliability and enhanced safety. By adopting leading solutions, FMs can transition from reactive maintenance to a proactive, intelligent strategy. As technology advances, predictive maintenance will continue to drive efficiency, sustainability and innovation across industries, making it an essential investment for modern facility management.
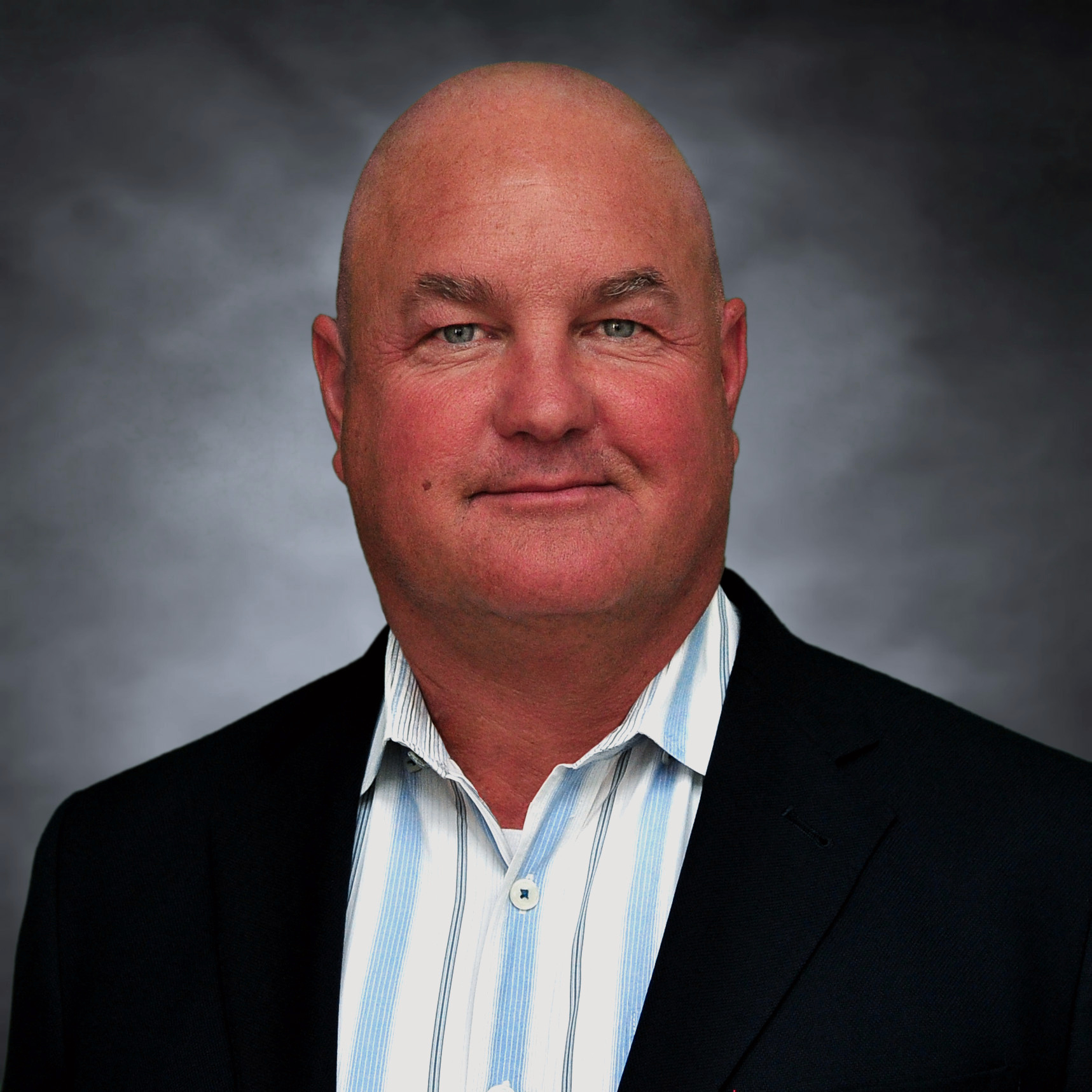
Dave Hopson, Ph.D., a founding partner of Triumphus, has 25 years of leadership experience in IT, with executive roles at Union Carbide Corp, BHP Billiton and Devon Energy. A retired United States Marine Corps team leader with expertise in special operations, he holds degrees from Sam Houston State University and Claremont Graduate School.
Read more on Operations & Maintenance and Technology or related topics Data strategy and information management , Maintenance Processes and Facility Technology
Explore All FMJ Topics