Roofing Sustainability
Aligning best practices with the 3 Ps
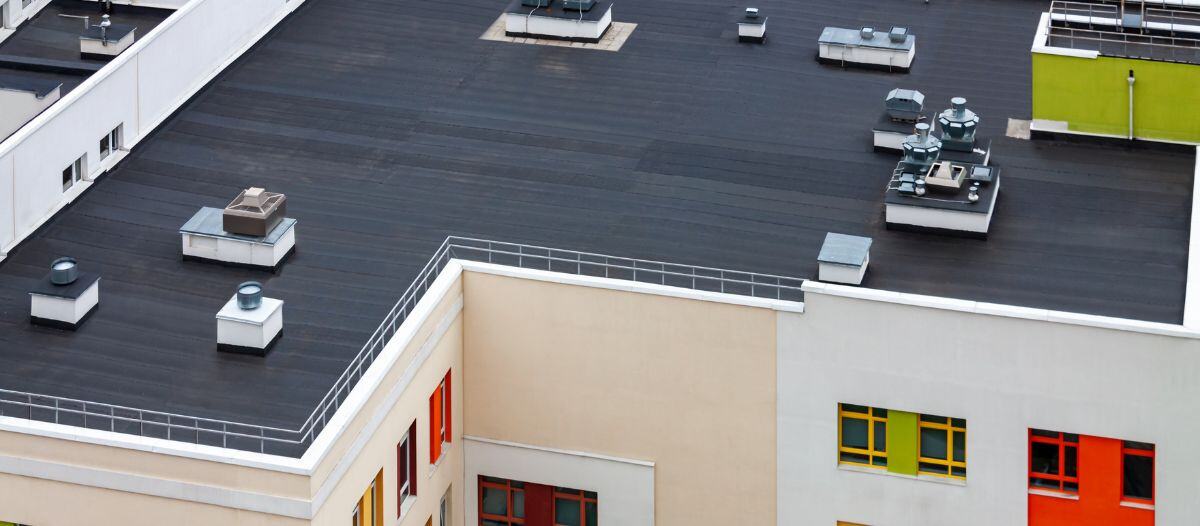
Sustainability is increasingly recognized as a critical focus in construction and facility management. Sustainability was originally defined as “using resources in a way that prevents depletion or permanent damage.” In the 1980s, the United Nations expanded this definition to mean “meeting the needs of the present without compromising the ability of future generations to meet their own needs.” This has become a cornerstone of sustainable thinking, especially in building design.
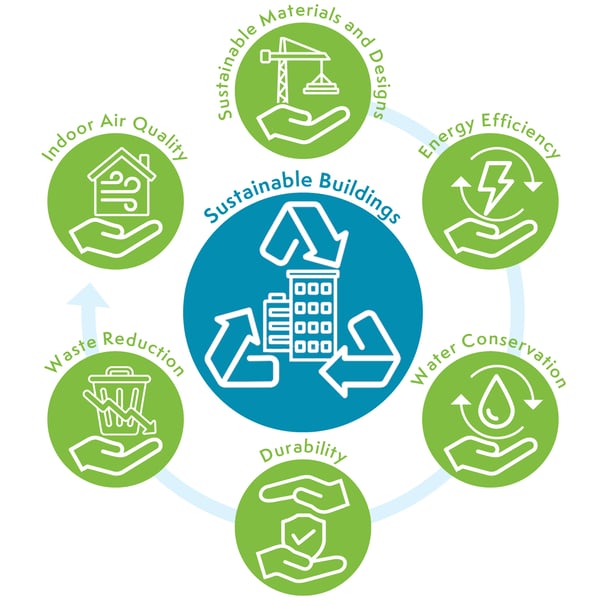
Sustainability is guided by the “three Ps: people, profit and planet.
-
People focuses on social equity for current generations while ensuring the same for future generations.
-
Profit aims for economic benefits and prosperity while focusing on resource efficiency.
-
Planet emphasizes environmental protection, ensuring resources for future generations. Keeping these principles in mind, sustainability in construction focuses on the use of sustainable materials, energy efficiency, water conservation, durability, waste reduction and indoor air quality (IAQ).
New construction often focuses on concepts like net-zero buildings and passive design -- constructing buildings that are safe and healthy for the occupants, fit the owner’s budget, have low life-cycle costs, and use responsibly resourced and long-lasting materials. When discussing sustainability in roofing, it is common to focus on big-picture concepts such as green roofs, stormwater retention and the use of solar panels. While these are important concepts, they can be cost-prohibitive and may be difficult (if not impossible) to incorporate in existing buildings. Keeping the three Ps in mind, there are many factors to consider in the design, construction, and life cycle phases to provide a sustainable roof system.
Design
A building’s roof, along with other enclosure components, is the first line of defense against the elements. It is important to design a roof that is appropriate for the building, keeping durability and longevity in mind.
Material selection
Material selection is key in sustainable roofing. Important factors include:
-
Recycled Content/Recyclability: was the material responsibly sourced and can it be recycled at the end of its lifespan?
-
Maintenance: systems requiring extensive maintenance will increase life cycle costs.
-
Weight: The building’s structure will put limitations on the weight of which roof materials can be utilized.
-
Slope: In low-slope assemblies, certain membranes offer better performance against ponding water. For steep-slope assemblies, manufacturers specify minimum slope requirements for specific materials.
-
Color: In warmer climates, light-colored and reflective membranes help prevent unwanted heat gain, whereas darker membranes are preferable in colder climates to retain heat.
-
Warranty: Generally, a longer warranty period will indicate a higher performing material or system.
Insulation (R-Value & attachment)
Energy efficiency is a pillar of sustainable construction. Roof insulation should be utilized to provide the minimum R-value dictated by the International Building Code (IBC).
Insulation attachment is often an overlooked aspect of roof construction. While fastening all layers of insulation is common, it can cause thermal bridging, as highly conductive metal fasteners transfer heat in or out of the building, reducing insulation efficiency. A better approach is to install insulation in multiple layers, fastening only the base layer and adhering the subsequent layers. This method helps create a barrier between the exterior air and the conductive fasteners, improving thermal performance.
Mechanical fasteners serve as a thermal bridge, reducing the R-value of the insulation assembly.
By separating the fasteners from the exterior with additional layers of insulation, thermal bridging is greatly reduced.
Fastening patterns are another commonly overlooked aspect of roof construction. The designer of record is responsible for determining the necessary number of fasteners based on factors such as building height and location. However, incorporating additional fasteners beyond the minimum requirement is a cost-effective upgrade that improves resistance to wind uplift, enhancing the durability and longevity of the roof system.
Cover boards & slope
Incorporating a coverboard into a roof system enhances wind uplift resistance, puncture resistance and overall durability, especially in regions prone to hail or on roofs that will experience significant foot traffic.
Slope is a crucial factor in roof design. The IBC mandates a one-fourth inch-per-foot slope for new construction, while re-roofing projects on existing buildings only require positive drainage. However, striving for a one-fourth-inch slope is advisable, as ponding water increases UV exposure, accelerating membrane degradation. Ensuring efficient water drainage is key to prolonging the roof’s lifespan.
Base flashings & penetrations
Base flashings and penetration flashings are typically the weakest component of a roof system. While the National Roofing Contractors Association (NRCA) and most manufacturers recommend a minimum flashing height of eight inches, increasing the flashing height can greatly enhance the roof’s durability with very little extra cost.
When designing penetration flashings, it is essential to choose durable, long-lasting solutions. Prefabricated or field-fabricated pipe boots typically outperform pourable sealer pockets (PSPs), which degrade under UV exposure and require frequent maintenance. Avoid relying on sealants, as they also deteriorate over time with UV exposure and demand ongoing upkeep. Instead, incorporate sheet metal counterflashings, storm hoods, and similar protective elements to enhance resistance against rain and UV damage.
Material compatibility
Understanding material compatibility is essential. With a focus on whole-building air and moisture barriers, tie-ins between several different materials are common. Understanding the compatibility of each of these materials is essential to avoid premature degradation of the waterproofing systems.
Always check material compatibility when tying together different materials. Here, the PVC caused an adverse reaction in the bituminous underlayment resulting in unsightly bitumen runs.
Temporary roof membrane
In construction, it is common to install the roof early to make the interior watertight, which often leads to significant foot traffic on the roof. This can cause issues like punctures and tears. A temporary roof membrane serves as a sacrificial layer, providing waterproofing but not intended as the final roof membrane. Once other trades have completed their work and foot traffic is minimized, the final roof system can be installed over the temporary membrane, avoiding the damage it would have incurred if installed earlier in the project.
Providing a temporary roof membrane can reduce foot traffic and subsequently reduce damage on a new finished roof membrane.
Ventilation
Indoor air quality is a key aspect of sustainability, and proper ventilation is essential for achieving this. Adequate ventilation is vital not only for the health of building occupants but also for the longevity of certain roof materials, such as asphalt shingles. Failing to provide adequate ventilation will usually result in premature failure of an asphalt shingle assembly.
Transitions to other systems
Roofs do not function in isolation; they must connect seamlessly with other building systems, such as windows, walls and mechanical units. When designing these transitions, it is essential to consider the long term. Many roofs installed today are designed for about 20 years, while windows and wall systems can last several years longer. Even when these systems have similar lifespans, they are often replaced at different times due to budget constraints. Without careful planning, systems that are still functional may need to be replaced to accommodate a new roof. For instance, when planning a clerestory window replacement before a roof replacement, ensure the windows are sized to accommodate the insulation thickness and base flashing requirements of the upcoming roof system.
Construction
A good design that incorporates strong sustainability principles is nothing if the construction is executed poorly. There are several measures to consider during construction to ensure a high performing, sustainable roof system.
Regular manufacturer & consultant visits
It is recommended to have the manufacturer visit the site at least three times during construction: at the beginning, middle and end of the project. These visits help assess the quality of membrane installation, inspect seams and identify any defects. Additionally, regular consultant visits are advised to ensure proper handling of transitions between the roof system and other building components.
Sequencing & protecting
Proper sequencing and protection are essential for every roof project. Only a section of the roof should be installed each day. The contractor should start installation in the areas farthest from the roof access and staging area to minimize foot traffic on newly installed sections. If this sequencing is not feasible, the contractor must provide robust protection, such as plywood and insulation boards, to safeguard the roof. Failure to properly sequence and protect the roof can lead to staining at best, or punctures and damage at worst.
Beware value engineering
Value engineering is defined as a systematic and organized approach to providing the necessary functions in a project at the lowest cost. While this can be a useful tool in meeting budgets, unfortunately the proposed substitutions are often not equal to the original design intent, therefore sacrificing functionality and quality. If value engineering is required to meet the project budget, it is important to thoroughly review all aspects of the proposed substitution to determine if performance will be affected.
Testing completed roofs
Infrared scans can show moisture within the roof system and help locate defects that may not be obvious to the naked eye.
Before a contractor is released from the site, it is good practice to test completed roofs. Infrared scans are highly effective for identifying issues within the membrane that are not visible to the naked eye. Another option is electronic field vector mapping, which creates an electric field on the roof; if there are punctures in the roof membrane, an electric current can pinpoint the location. Spray tests, like the AAMA 501.2, simulate a rain event in a controlled manner, making them excellent for testing waterproofing assemblies.
Life cycle
The lifecycle phase is where the design and construction are complete, the building is turned over to the owners. Decisions play a significant role in maintaining the sustainability of the roof. Durability, waste reduction and IAQ are areas where actions can have a lasting impact.
Maintenance
Regular maintenance is crucial for roof assembly. Failure to provide regular maintenance can void a warranty and lead to premature roof failure. Leaking roofs can cause structural damage, mold growth and air quality issues, so it is vital to stay proactive.
When conducting maintenance, it is essential to use someone with a trained eye to spot potential issues before they escalate. Issues like membrane punctures, sealant failures or poor transitions with other systems may not always be obvious but can cause significant damage over time. Educate anyone who accesses the roof on best practices to avoid causing damage and remember that roofs are interconnected with other building systems. Leaks from windows, walls, or mechanical equipment can infiltrate the roof and cause premature failure.
Reducing waste
Addressing the waste reduction principle, consider that roofing contributes to approximately 40 million tons of solid waste in U.S. landfills each year, accounting for 5 percent of all solid waste. Making choices that extend a roof’s lifespan is the most sustainable approach. Roof coatings are a great option; they act as "sunscreen" for buildings, providing UV protection for the existing membrane. They make financial sense if less than 25 percent of a roof needs repair — beyond that, replacement is more cost-effective.
Another option is overlaying, where a new roof is installed over the existing one. This approach is exempt from code requirements for R-value upgrades, though it offers the opportunity to provide additional insulation if desired. Like coatings, overlays are financially viable if less than 25 percent of the roof needs repair.
Reuse & recycle
Finally, prioritize reuse and recycling whenever possible. For example, reusing existing insulation can save substantial costs and keep large amounts of material out of landfills. Many roofing materials are now advertised as recyclable, so explore these options and look for programs or recycling centers in the area.
In conclusion, sustainability in roofing encompasses much more than just the implementation of green roofs and stormwater management systems; it is about designing durable, energy-efficient roof systems and ensuring proper installation and ongoing maintenance throughout their life cycle. By taking proactive measures, such as regular inspections, implementing waste reduction strategies and prioritizing reuse and recycling, the life of the roof can be significantly extended while also saving money and contributing to environmental conservation. The owner's role is crucial in maintaining the roof's performance and sustainability, ultimately benefiting both the building and the planet.
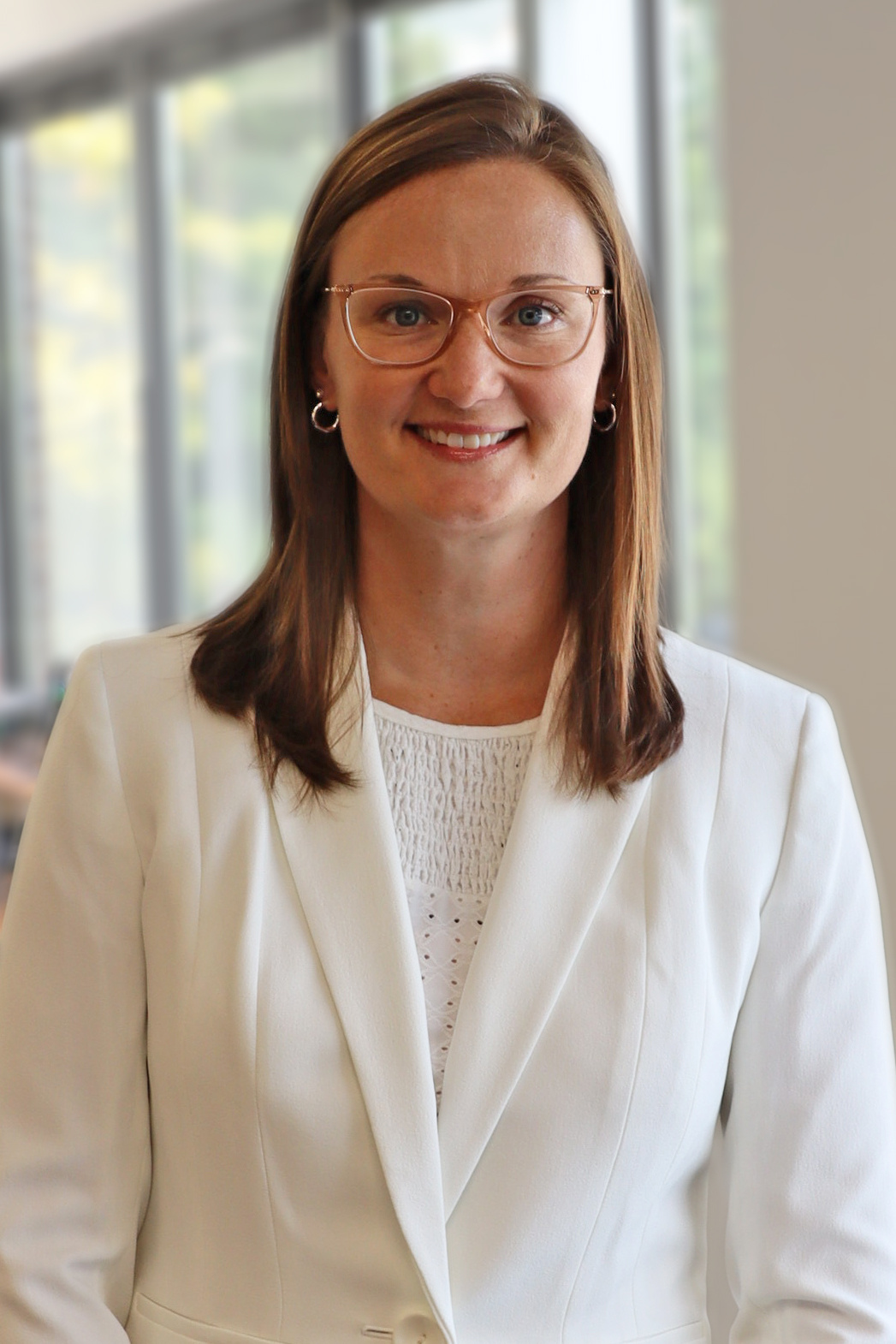
Sherre Bartlett, AIA, CDT, performs evaluations, design and construction phase services related to the building enclosure (roof, wall, window, waterproofing) systems. She is experienced in the preparation of engineering studies, reports, cost estimates, specifications and drawings. She provides construction administration services, including attendance at pre-construction meetings and progress meetings; review of product submittals, shop drawings, and construction schedules; preparation and review of field reports and deficiency logs, and review of project closeout. Bartlett is knowledgeable with the installation and performance of roof, waterproofing, and air and thermal barrier system types: built-up roofing (BUR), modified bitumen, single ply (PVC, TPO, EPDM), kettle modified, fluid applied, spray applied foam systems, and various sloped roof systems (shingles, metal, slate, etc.). She is familiar with façade and curtain wall systems: brick masonry; concrete block; metal wall panel; composite wall sheathing on concrete, wood and steel framed buildings; and glass and metal curtain walls.
Read more on Project Management , Operations & Maintenance and Sustainability or related topics Project Management and Best Practices
Explore All FMJ Topics