The Hidden Costs of Conventional Cleaning
Why sustainable solutions are the future
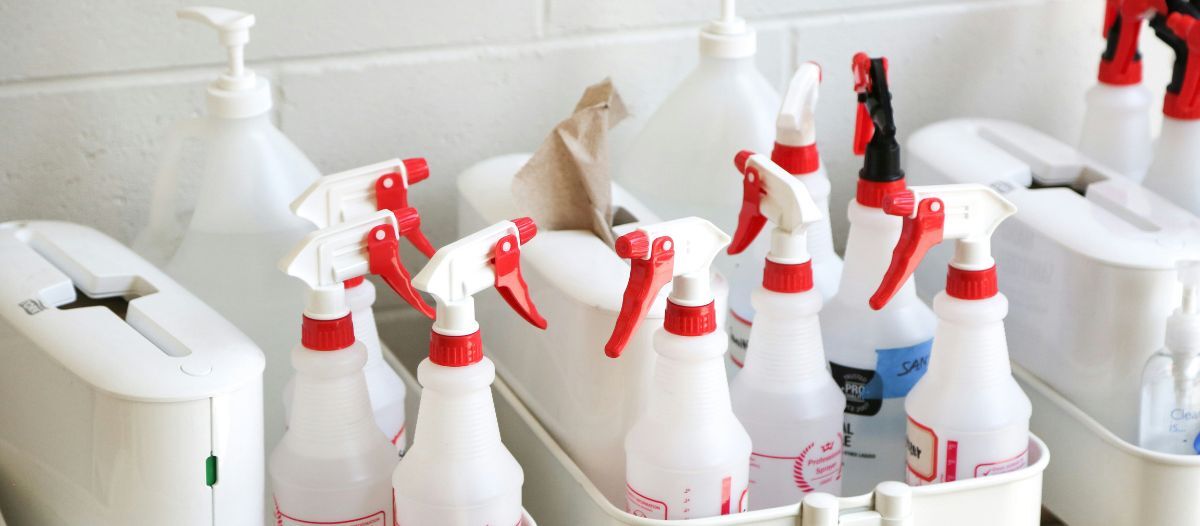
For businesses striving for sustainable operations, traditional cleaning techniques pose significant challenges. Traditional chemical-based cleaning methods may inadvertently jeopardize the primary goals of any cleaning program, which are safety, infection control and asset longevity. The risks of hazardous exposure and the rapid deterioration of facility assets make the shift to safer, more sustainable practices more crucial than ever.
The impact
Strong surfactants, volatile organic compounds (VOCs) and other chemicals present in many traditional cleaning products can degrade indoor air quality (IAQ) and pose health risks. Workers who regularly use these products may develop breathing issues, skin irritation or asthma. Over time, exposure to chemical fumes and residues can cause neurological damage in addition to headaches and vertigo.
Chemical exposure is not only a risk for the cleaning crew. Building occupants can also be exposed to chemicals that remain on surfaces and in the air. In environments such as hospitals and assisted living facilities, where individuals may have compromised immune systems, these exposures may exacerbate preexisting health conditions and impair overall health.
Serious health consequences may result from prolonged exposure to VOCs. These compounds are linked to an increased risk of neurological deficits, allergic responses and respiratory disorders. Because they easily evaporate into the atmosphere, they also contribute to interior air pollution. VOCs are particularly dangerous in enclosed places, such as offices, classrooms and medical facilities, where insufficient ventilation can lead to the buildup of hazardous airborne chemicals.
Studies show that VOCs from cleaning products are the primary cause of indoor air pollution, which can be up to five times higher than outdoor air. Facility managers must consider not just the immediate cleaning effectiveness of the materials, but also the long-term health consequences on the people who regularly use the space. The IAQ and general health of residents and employees can be significantly enhanced by switching to nontoxic alternatives.
Having high-quality indoor air in places like businesses, hospitals and schools helps to prevent disease, maintain a comfortable, healthy environment, and reduce absenteeism. Reducing the use of cleaning products that contain VOCs can significantly enhance IAQ and infection prevention.
Issues with preventing infections
Infection prevention requires strong disinfectants, but many conventional products include dangerous ingredients like quaternary ammonium compounds (quats). These substances must be handled carefully to prevent adverse effects, which entails having adequate airflow and donning personal protective equipment (PPE).
Antimicrobial resistance brought on by excessive use of these potent disinfectants can eventually make it more difficult to eradicate harmful bacteria. Additionally, some chemical disinfectants cause protective biofilms to form, which makes it easier for opportunistic infections to spread. This implies that rather than preventing infections, some common cleaning methods may be inadvertently contributing to outbreaks. FMs have a responsibility to combine the need for effective disease control with the need to ensure resident and staff safety.
Facility durability
Harsh chemical cleansers, particularly those that contain bleach, ammonia or acidic compounds, can hasten the deterioration of facility assets. Frequent exposure to these chemicals can cause floors, carpets, countertops and fixtures to become discolored, warp and deteriorate prematurely. Metal surfaces – including kitchen appliances, medical equipment and doorknobs – are particularly vulnerable to corrosion when exposed to powerful disinfectants over time.
These effects not only lower a facility's aesthetic attractiveness but also increase maintenance costs. The need to replace and repair equipment that has been damaged by conventional chemical-based cleaning methods places a strain on operating budgets and sustainability goals.
The consequences extend beyond visible degradation. The protective coatings on floors and fixtures deteriorate when aggressive cleaning solutions are used, making surfaces more porous and susceptible to bacterial and stain growth. As a result, more extensive cleaning and repair work is required, which drives up costs even further. Additionally, it is often necessary to replace broken fixtures and equipment too soon, leading to wasted spending and higher capital costs.
By switching to noncorrosive cleaning products, organizations may protect their investments, increase the lifespan of their infrastructure and reduce operational downtime.
Examining a facility for toxic chemicals & outdated procedures
The transition to sustainable cleaning practices begins with a facilities audit. This process helps identify whether dangerous chemicals or outdated cleaning methods are being employed and provides a roadmap for improvement.
FMs should review all of the cleaning products being used and check the labels for hazardous ingredients including ammonia, chlorine, quats and VOCs. Safety data sheets (SDS) contain more details on potential exposure risks and hazards. Additionally, examining the cleaning practices and training materials already in use may reveal inefficiencies or risky activities.
Another essential component of the audit is looking at staff health records, surface lifespan and IAQ for patterns in respiratory issues, skin irritation or other symptoms linked to chemical exposure. Air quality studies and swab testing can provide information on residual contaminants left by conventional cleaning agents. Once problem areas have been identified, FMs might opt to seek alternative cleaning solutions that promote sustainability goals while preserving efficacy and safety.
FM’s shift to sustainability
The importance of sustainability to today's consumers and businesses is growing. Businesses are under growing pressure to reduce their environmental footprint without compromising their ability to operate effectively.
As climate change becomes a more pressing global issue, businesses are facing mounting pressure to reduce their carbon impact. Sustainable cleaning is not just a trend but an essential shift to more cost-effective, environmentally responsible and healthful practices.
Green cleaning methods usually result in long-term cost savings for businesses. Less wear and tear on facility equipment, lower disposal costs and fewer chemical purchases all affect financial efficiency. By helping companies comply with legal and sustainability requirements, sustainable cleaning programs help them build their brand and draw in environmentally conscious stakeholders.
Available options
One of the best options for companies looking to go green is e-water, often referred to as electrolyzed water. This nontoxic, noncorrosive cleaning and disinfection approach is produced with salt, water and electricity. E-water is safe for both cleaning personnel and building occupants because it does not leave behind harmful residues or strong aromas like other chemical cleansers do.
It has been demonstrated that e-water effectively eradicates bacteria, viruses and other pathogens without causing antimicrobial resistance. Because of its broad-spectrum effectiveness, facilities may maintain high levels of hygiene without putting people in danger from the side effects of traditional disinfectants. Because of its pH balance and absence of corrosive substances, e-water protects assets by preventing damage to flooring, counters and fixtures. Fewer repairs and replacements are required, which makes it an affordable alternative.
Another important advantage is the environmental impact — or lack thereof — of electrolyzed water. A facility's carbon footprint is greatly decreased because the cleaning and disinfecting solutions are produced on site and do not require transportation, single-use plastic packaging or disposal as hazardous waste. E-water can be a sensible and responsible option, as it supports green construction goals and aids in obtaining sustainability certifications.
The way forward
Facility management will continue to evolve as the globe moves toward a more sustainable future. By offering automation and predictive insights, the combination of big data analytics, machine learning and artificial intelligence may strengthen sustainability initiatives even more. Organizations must constantly develop new concepts and implement sustainable facility management best practices to comply with ever-tougher environmental laws.
FMs may contribute to a cleaner, safer future by reevaluating conventional cleaning methods and introducing eco-friendly substitutes. Additional advantages of this include a longer asset life, lower operating costs and healthier environments.
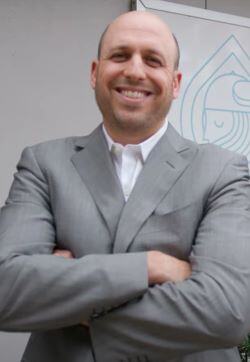
Joshua Schwartz is president and co-founder of Viking Pure and is an active developer of medical real estate and supportive housing. Prior to Viking Pure, Schwartz was the president of an Article 28 Diagnostic and Treatment Center. He began his career in the financial industry, first in investment banking at Citigroup; then at private equity firm Apollo Management. Schwartz graduated Phi Beta Kappa from Yale College with a bachelor’s degree in economics with distinction and holds a master’s degree from New York University, where he graduated with honors.